Did you know that the order-picking process is reported to account for 50-55% of the total warehouse operating cost? That’s a large percentage!
But there’s hope – in the evolving landscape of warehousing and logistical management, automated picking systems have emerged as a game-changer. They have streamlined several processes, increasing efficiency and accuracy in order fulfillment. But to leverage the full potential of these advancements, it’s essential to understand how they operate and how the landscape has evolved.
In this article, we’ll discuss:
- What is an automated picking system?
- Benefits of picking automation
- The evolution of picking technology
- Types of automated picking systems
- Choosing the right system for your warehouse
What is an Automated Picking System?
Automated picking system: automated retrieval of items from storage to a nearby processing area before shipment that utilizes software and machinery such as goods-to-person systems, AMRs, and more. These capabilities are further bolstered by the integration of robotic arms, which autonomously manage the handling of loads.
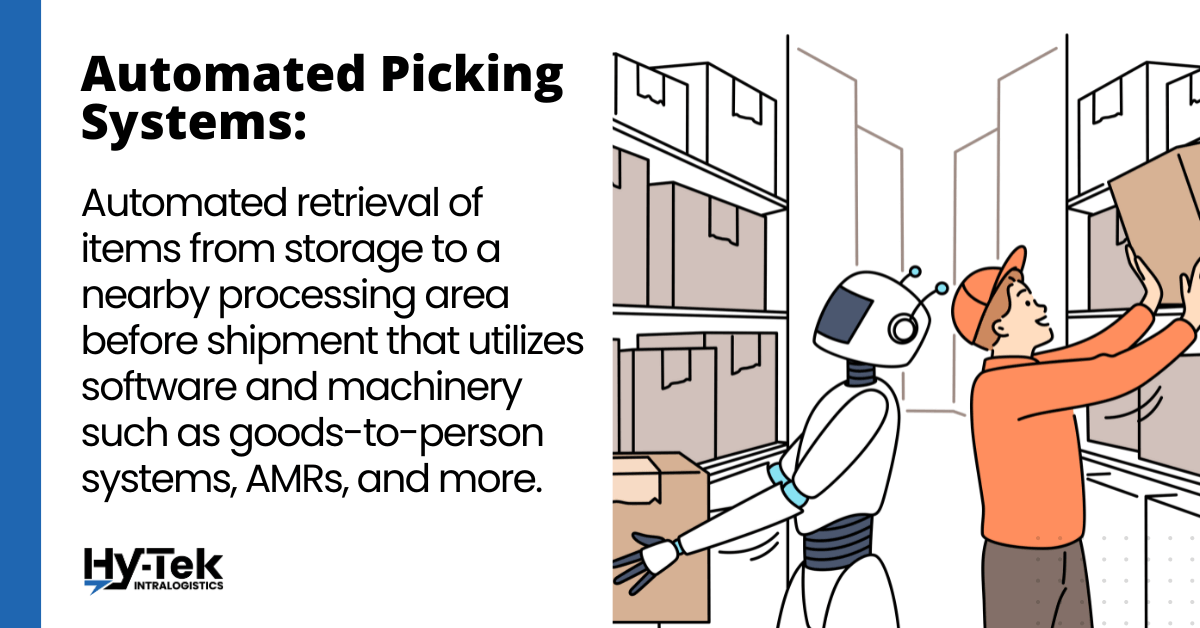
Benefits of Picking Automation
By automating the picking process, warehouses can handle higher volumes of orders with greater speed and accuracy. This technology has revolutionized the logistics and supply chain industries, enabling businesses to meet the growing demands of e-commerce and improve overall operational efficiency.
Key advantages include:
- Efficiency Boost: Automated systems drastically reduce item retrieval time, resulting in streamlined processes and improved supply chain efficiency.
- Space Optimization: These systems intelligently organize storage, utilizing advanced algorithms to maximize available space, accommodating more inventory, and enhancing order fulfillment.
- Error Reduction: Manual errors like incorrect picks or miscounts are minimized through automation, leading to higher customer satisfaction and fewer discrepancies.
- Real-time Inventory Visibility: Integration with inventory software that provides up-to-the-minute stock updates, mitigating the risks of stockouts or overstocking.
- Versatile Handling: Automated systems adapt to diverse products, accommodating different shapes, sizes, and weights across industries like pharmaceuticals, retail, and automotive.
- Safety: By reducing manual lifting and handling of heavy items, automated systems create a safer working environment, lowering the risk of injuries and related costs.
In summary, automated picking systems revolutionize warehousing by enhancing efficiency, minimizing errors, optimizing space, and ensuring workplace safety. As technology advances, these systems will continue to evolve, reshaping how goods are retrieved and distributed.
The Evolution of Picking Technology
A Brief History of Picking Systems
The history of picking systems dates back to the era of manual picking. It was labor-intensive and fraught with human errors. Warehouse workers would spend hours manually searching for and retrieving items from shelves, often leading to delays and inaccuracies in order fulfillment.
Barcodes were invented in the 1940’s, however, the first implementation was in June of 1974 where the first handheld scanning device was installed at a Marsh’s supermarket in Troy, Ohio.
Did you know that the first product to be barcoded was Wrigley’s Gum?
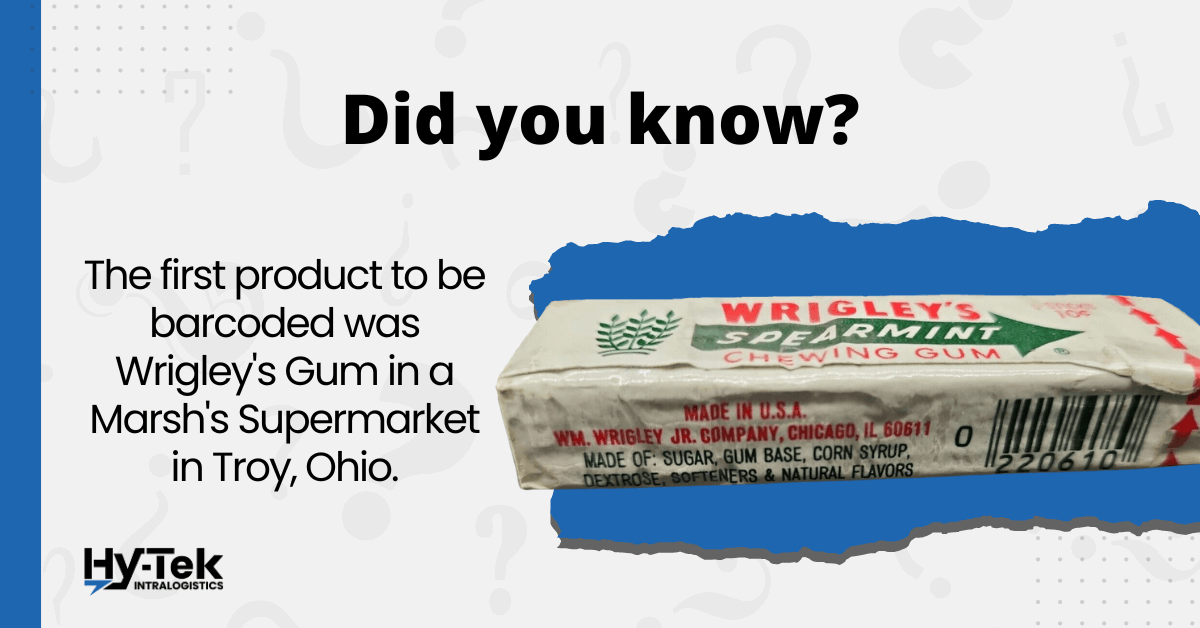
The advent of barcoding in the 1970s marked a turning point by bringing rudimentary automation to picking. Barcodes allowed for the identification and tracking of individual items, enabling workers to use scanners to quickly locate and pick the correct products. This technology significantly improved efficiency and reduced errors in the picking process.
However, it was only in the late 20th and early 21st century that dramatic strides in technology ushered in advanced automated picking systems we know today.
Technological Advancements in Automated Picking
Advancements in technology, ranging from sophisticated software to diverse sets of hardware, have reshaped automated picking. These innovations have revolutionized the way warehouses and distribution centers operate, enabling faster order fulfillment, increased accuracy, and improved overall productivity.
One of the key technological advancements in automated picking is the development of warehouse management software (WMS). WMS systems integrate with various hardware components and provide real-time visibility into inventory levels, order statuses, and warehouse operations. They optimize picking routes, allocate resources efficiently, and enable seamless coordination between different areas of the warehouse.
Robotics have also played a crucial role in the evolution of automated picking systems. Autonomous mobile robots (AMRs) and robotic arms equipped with advanced sensors and algorithms can navigate warehouse aisles, pick items from shelves, and transport them to designated locations.
These robots work collaboratively with human workers, taking on repetitive and physically demanding tasks, while humans focus on more complex decision-making and supervision. The integration of robotics in picking systems has not only increased efficiency but also improved worker safety and ergonomics.
Now let’s delve into the other types of automated warehouse picking systems, each possessing unique functionalities and applications.
Types of Automated Picking Systems
Automated picking systems have revolutionized warehouse operations, making them more efficient and productive. These systems utilize advanced technologies to streamline the picking process, reducing errors and saving valuable time. Let’s explore some of the different types of order-picking systems:
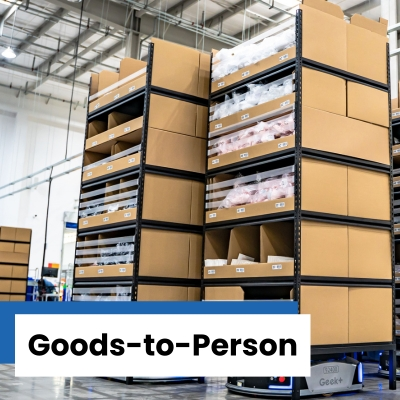
1. Goods-to-Person Picking:
The Goods-to-Person picking approach brings items directly to the operator, eliminating the need for them to navigate vast warehouse spaces. This not only saves time but also improves ergonomic working conditions for the warehouse staff.
In a Goods-to-Person system, automated storage and retrieval technologies play a significant role. Machines deliver storage units to the workstation, where operators can pick the required items. These machines are equipped with sophisticated algorithms that optimize the delivery routes, ensuring maximum efficiency.
- Enhances productivity by minimizing picker movement.
- Reduces physical strain on operators.
- Ideal for high-density storage environments.
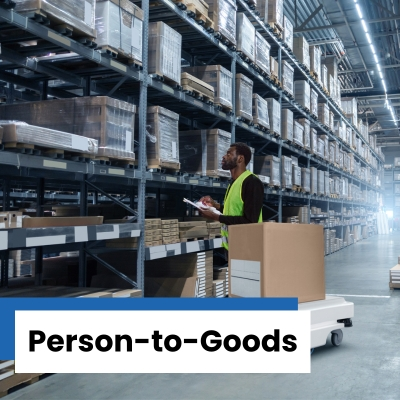
2. Person-to-Goods Systems:
A person-to-goods system is a system where autonomous mobile robots and human pickers work side-by-side. The robot will autonomously route to the specific pick location. The picker will meet the robot at the pick location, pick the item from the storage location, and place it in the tote that the robot is carrying.
It can be optimized using software to ensure the most efficient picking path and minimize travel time.
- Suited for large warehouses with ample space for picker movement.
- Offers flexibility to adapt to changing layouts.
- Efficient for low-density storage areas.
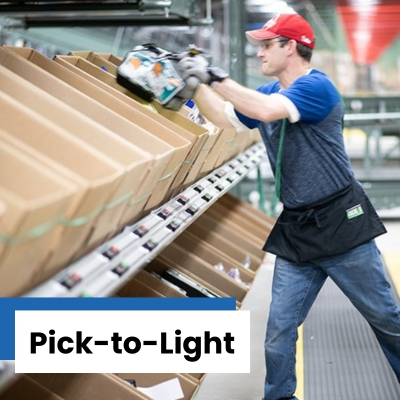
3. Pick-to-Light System:
Pick-to-Light systems employ an array of light modules mounted on racking. When an operator is ready to pick an item, the corresponding module lights up, indicating the exact location of the item.
These visual cues significantly speed up picking times and reduce errors, thereby increasing operational efficiency. Operators can quickly locate items without the need for extensive training or constant reference to paper instructions. Pick-to-Light systems are especially effective in environments where a high volume of small items needs to be picked accurately and rapidly.
- Reduces training time for new pickers.
- Minimizes picking errors.
- Well-suited for environments with high SKU variety.
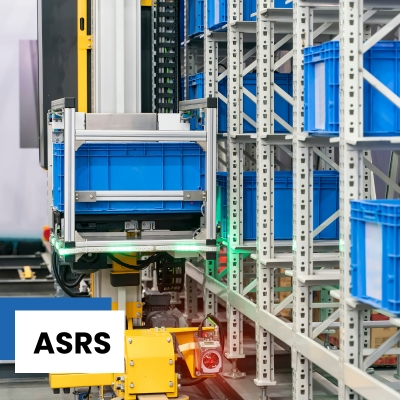
4. Automated Storage and Retrieval Systems:
AS/RS systems use a system of shuttles and conveyors to store and retrieve items automatically. They optimize space usage and speed up the retrieval process.
- Maximizes vertical space utilization.
- Ensures accurate inventory control.
- Ideal for high-density storage and time-sensitive operations.
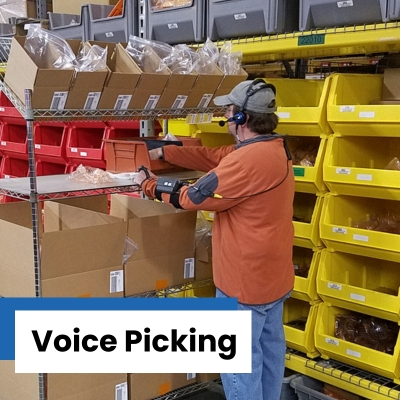
5. Voice-Directed Picking:
Voice-Directed Picking uses speech recognition and synthesis to interact with the operator. Operators receive verbal instructions via a headset, directing them to item locations and specifying the quantities needed.
- Enhances picker mobility and safety.
- Reduces errors caused by distractions.
- Suitable for environments with varying item sizes.
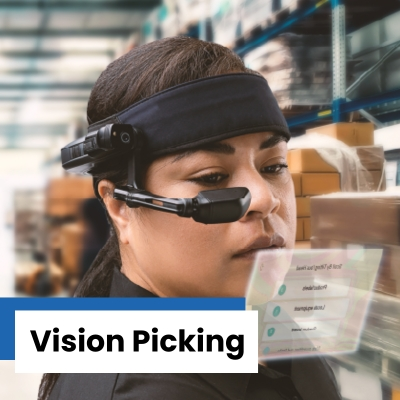
6. Vision Picking:
Utilizing augmented reality or smart glasses, vision-picking systems overlay digital information onto the picker’s field of view, guiding them to the correct items.
- Streamlines complex picking processes.
- Reduces training time for new employees.
- Well-suited for warehouses with diverse and complex item assortments.
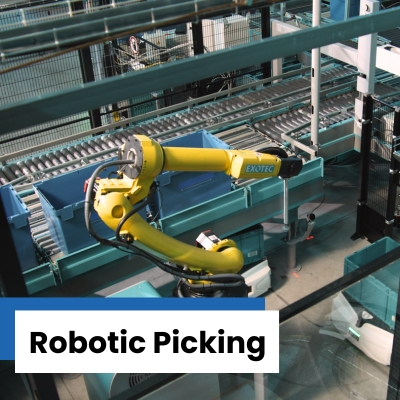
7. Robotic Picking System:
These advanced pick-and-place robots utilize advanced computer vision and gripping technologies to identify and handle items within the warehouse.
They are particularly effective when paired with goods-to-person systems. In this instance, the goods-to-person system should now be called “goods-to-robot.” As the name might suggest, the robot replaces the human picker and retrieves items from the totes that are presented to it.
- High-speed and precise picking.
- Ideal for repetitive, high-volume tasks.
- Can adapt to different item shapes and sizes.
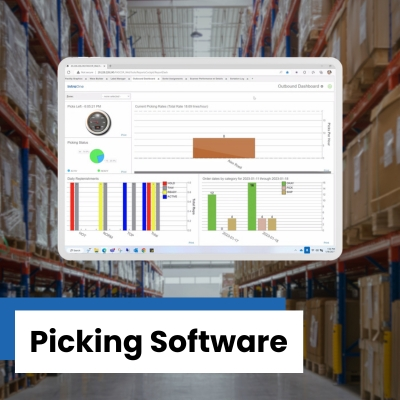
8. Picking Software:
Picking software encompasses a range of digital tools that optimize order-picking processes, route planning, and inventory management, increasing efficiency and accuracy.
- Allows real-time inventory tracking.
- Optimizes picker routes for time savings.
- Adaptable to various warehouse types and sizes.
Choosing an Automated Picking System
When considering the implementation of automated picking systems for your warehouse, several crucial factors come into play to ensure successful integration and operation. These factors encompass:
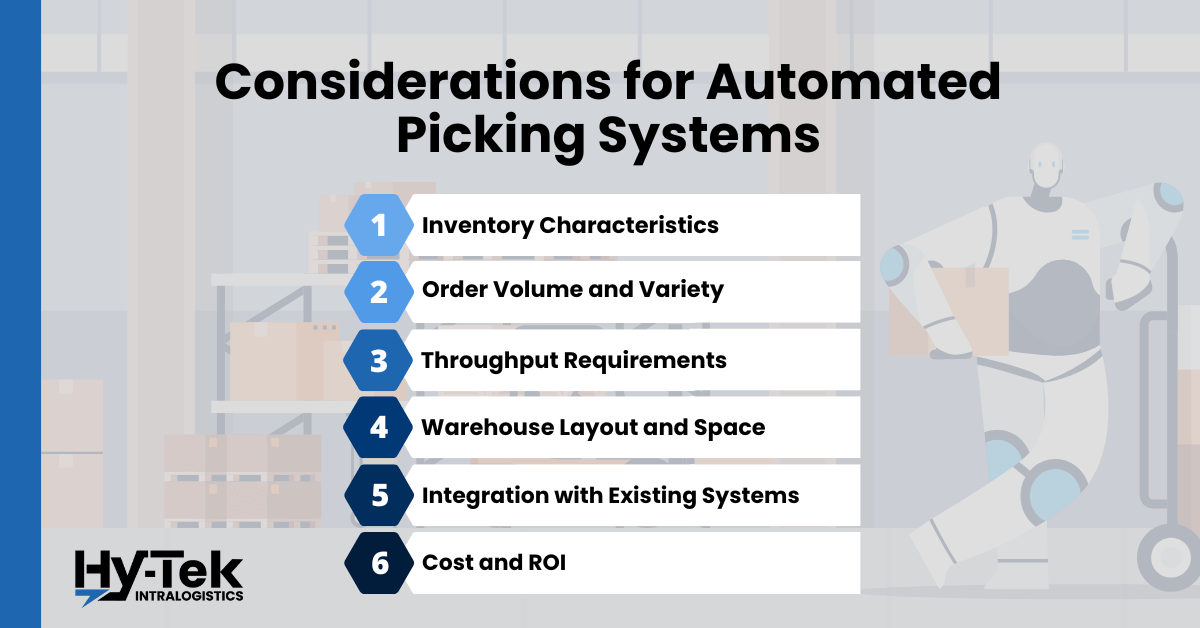
- Inventory Characteristics: Analyze your product range, sizes, shapes, and weights. Automated systems should accommodate the diversity of items you handle.
- Order Volume and Variety: Evaluate the volume and variety of orders you process daily. Choose a system that aligns with your order profiles, whether they involve large quantities of a few items or a wide range of products.
- Throughput Requirements: Determine the expected picking rate and processing speed needed to meet demand. The system should be capable of handling your peak periods.
- Warehouse Layout and Space: Assess your warehouse layout and available space. Consider how automated equipment fits within your existing infrastructure while optimizing storage capacity.
- Integration with Existing Systems: Ensure seamless integration with your current inventory management, order processing, and warehouse management systems. Compatibility is crucial for smooth operations.
- Costs and ROI: Calculate the upfront investment, including equipment, installation, and training. Balance this against the anticipated return on investment through increased efficiency and reduced labor costs.
- Maintenance and Support: Consider the ongoing maintenance requirements and availability of technical support. Reliable support is essential to minimize downtime and disruptions.
- Scalability: Choose a system that can scale as your business grows, accommodating future expansion and changes in demand.
- Employee Training: Assess the training needs for your workforce to operate and manage the new automated system effectively.
- Operational Flexibility: Ensure the system can adapt to changing order profiles, seasonal demands, and evolving business strategies. Here’s 4 tips to identify flexible automation.
- Safety: Prioritize the safety of your employees and automated equipment. Systems should be designed to minimize risks and adhere to safety regulations.
- Vendor Reputation: Research and select a reputable vendor with a proven track record in providing reliable automated picking solutions.
- Data Analytics: Consider systems that offer data analytics capabilities to monitor performance, identify bottlenecks, and make informed decisions for continuous improvement.
Partnering with an experienced robotic systems integrator can be the pivotal step toward unlocking the full potential of automated picking systems and ensuring a seamless implementation process.
These experts bring a wealth of experience in designing, deploying, and optimizing automated solutions tailored to your warehouse’s specific requirements. Their in-depth knowledge spans not only the technology but also the intricacies of your operations, leading to efficient system integration and minimized disruptions.
By collaborating with a trusted systems integrator, you can navigate complexities, mitigate challenges, and accelerate the realization of your return on investment (ROI). Their expertise not only streamlines the implementation process but also provides ongoing support, fine-tuning, and scalability adjustments, ultimately positioning your warehouse for sustained success in a rapidly evolving business landscape.