AGVs – When does it make sense?
AGVs can be equipped for a variety of loads and applications. There are various navigation and guidance systems (wire-guided, recessed magnetic bars, magnetic tape, visual recognition, or laser-guided) each with its own advantages and disadvantages. This blog explores when an AGV solution might make sense in your operations.
AGVs or Automatically Guided Vehicles are increasingly being used in operations all over the world to improve safety, reduce operating costs and improve operational efficiencies. They can be used in a variety of applications:
- Transport Small Loads (examples could be parts delivery in manufacturing, laundry or food service delivery in hospitals, mail or files in offices)
- Transport Unit Loads (examples could be pallets, large containers, or roll handling) – can be equipped with conveyor surface or fork truck style AGVs)
- Tuggers (examples could be drive units to pull carts or trailers forming a train-like system)
- Custom Applications (examples could be flexible manufacturing or assembly line transport/indexing)
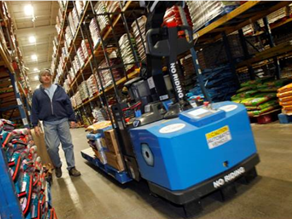
Companies are always looking for ways to reduce costs. Let’s look at Unit Load Transportation as one example. When you consider a forklift operator accounts for nearly 70% of the operating costs over the life of a vehicle, one could drastically reduce labor costs by deploying AGVs where possible. Forklifts require an operator to move product from point A to point B whereas AGVs do not. Operators take breaks, eat lunch, chat with co-workers, call in sick and take vacations whereas AGVs do not. Manned forklifts are by default, unpredictable and can possibly cause product or facility damage whereas AGVs are fully predictable and do not cause damage. Deploying AGVs for non-value added, repetitive travel allows companies to better utilize personnel for value-added operations.
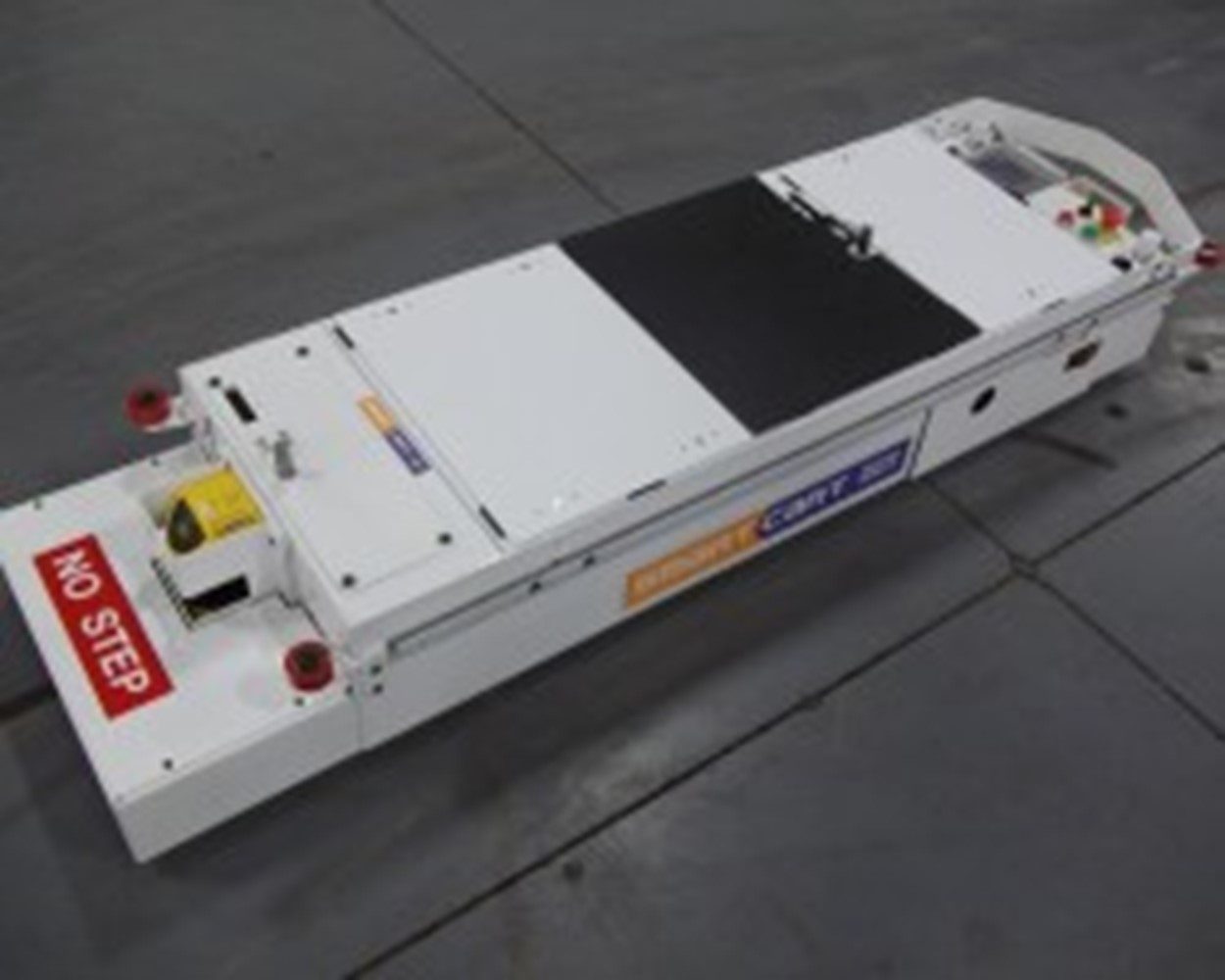
Advantages of AGVs
- Predictable, safe operation
- Traffic management system guaranteed to avoid collisions
- Effective optimization of transport flows according to fleet available, traffic conditions, and transport missions
- Flexible
- No infrastructure required
- Scaleable – number of AGVs can be increased as the business grows
- Routes are easily reconfigured, depending on the type of guidance system
- Workflow shared efficiently and dynamically between AGVs in the system
- Efficient and Reliable
- No destination or schedule errors
- Allows more precise inventory management, just-in-time delivery
- Operates 24/7 with little to no human intervention
- Elimination of barriers
- Unlike conveyor systems, AGVs only block access while traveling through an area or while stationary in a station
- Less potential for System Downtime
- Maintenance is scheduled for individual units, allowing the remaining units to continue to work
- Unplanned failures only impact individual units, not the entire system
AGVs can be equipped for a variety of loads and applications. There are various navigation and guidance systems (wire-guided, recessed magnetic bars, magnetic tape, visual recognition or laser-guided) each with its own advantages and disadvantages. As with other material handling applications, one size does not fit all. Each application requires many factors to be taken into consideration when developing the right AGV solution. Want to take advantage of the many benefits related to the use of AGVs?… a call to Hy-Tek Material Handling’s Integrated Systems Division is a great place to start!
What does AGV Stand for?
AGV stands for Automatically Guided Vehicle
What is an AGV?
There are several types of AGVs. These include:
Automated carts – The simplest kind of AGV with minimal features for lowest cost implementation.
Unit load AGVs – Individual vehicles that transport loads (typically pallets, bins, carts or bundles) on forks or on the AGV’s deck. Roll-handling AGVs specifically handle heavy rolls of steel or paper.
Tugger AGVs – Powered units pulling a series of non-motorized trailers that each carries a load.
Automated forklift AGVs – An existing forklift truck whose controls have been converted to allow unmanned operation
How Can AGVs be Used?
Transport Small Loads (examples could be parts delivery in manufacturing, laundry or food service delivery in hospitals, mail or files in offices)
Transport Unit Loads (examples could be pallets, large containers, or roll handling) – can be equipped with conveyor surface or fork truck style AGV’s)
Tuggers (examples could be drive units to pull carts or trailers forming a train like system)
Custom Applications (examples could be flexible manufacturing or assembly line transport/indexing)
What are the Benefits of AGVs?
Accountability – Once a product is onboard an AGV, it is tracked so “lost” or misplaced product will be minimized
Automatic line balancing – In a production environment with multiple operations conducted at varying times, AGVs can assist in line balancing
Cost control – An AGV system’s costs are very predictable, while labor costs tend to increase and can change quickly depending on local economic conditions
Facility maintenance – Collision avoidance capabilities prevent damage within the facility
Flexibility – An AGV’s path can be changed as production and handling needs evolve
Fewer restrictions – Free-roaming, AGVs eliminate access issues created by conveyors and require less space than conventional forklifts, allowing for narrower aisles
Reduced operating costs – Charging and battery handling can be automatic with an AGV system and the controlled acceleration/deceleration minimizes wear on components
Reduction in product damage – AGVs handle products gently, reducing scrap and waste
Repeatability – AGVs perform repetitive movement tasks predictably and reliably
Safety – AGVs always follow their guide path and stop if they encounter an obstruction, improving the safety of surrounding personnel
Scheduling – Because of their reliability and on-time delivery, AGVs improve scheduling capabilities and the efficiency of operations
Scalability – More AGVs can be added to expand capacity and throughput