Imagine a warehouse where every item you need is just a few clicks away. That is the beauty of Goods-to-Person Picking Systems (G2P or GTP). These innovative automated systems are revolutionizing the world of order fulfillment by streamlining the process and boosting productivity.
With G2P systems, you no longer need to waste time wandering around looking for items. Instead, the system brings the items to you. The process is simple: a worker requests an item, and the G2P system sends it to a picking workstation, where it is retrieved and taken to a designated packing location for shipment. This saves time and increases accuracy, making it a cost-effective solution for businesses of all sizes.
GTP systems can be easily integrated with other picking technologies, including pick-to-light, warehouse software, a takeaway conveyor, or a robotic arm for piece picking.
Whether you are a consumer interested in the latest innovations or a business looking to optimize your supply chain, this blog will provide valuable insights into the exciting world of G2P technology.
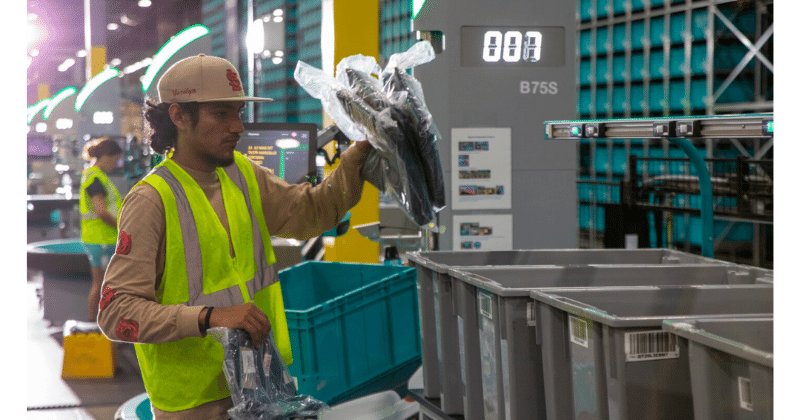
What is Goods to Person Picking?
Goods-to-person systems can also be categorized as a subcategory of Automated Storage and Retrieval Systems (ASRS). What differentiates an ASRS from a G2P system is that the goods are delivered directly to the picker, and then returned to storage. A shuttle for example may be used to temporarily store a case of goods and then dispense it to an outbound conveyor for palletization. In this scenario, the shuttle stores and retrieves but does not provide goods to a picker.
Process wise a G2P system functions like any other ASRS. When an order comes in, the system receives instructions to retrieve specific products from storage and deliver them to the operator. The system transports the necessary bin, tote, or pallet to picking workstations, where the operator can easily access the required product. The operator confirms the pick, and the system updates inventory levels automatically.
Benefits of Goods to Person Picking
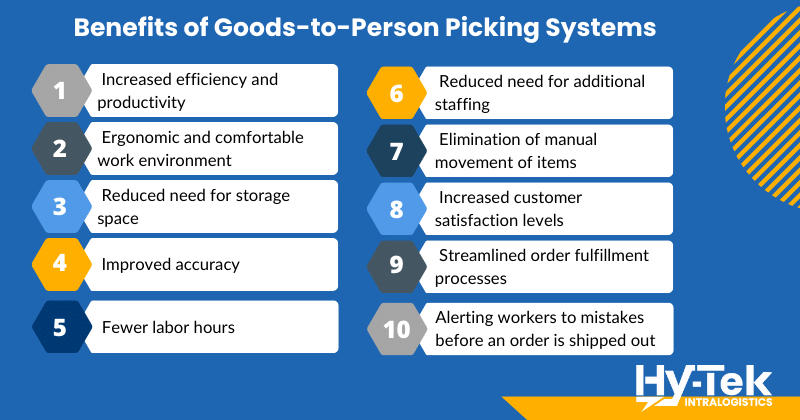
There are many benefits of implementing a goods-to-person order-picking system. These solutions can improve productivity and efficiency while reducing labor costs. Also, these systems can help reduce errors during the picking process.
The goods-to-person approach is both flexible and efficient, as it can handle multiple stock-keeping units (SKUs) with no manual intervention required. Unlike traditional manual picking or Person-to-Goods systems, the operator isn’t required to physically move to the product. In addition, its scalability allows it to be adapted to several types of warehouses, making it an ideal solution for many different operations.
Other benefits of G2P systems include:
· Increased efficiency and productivity through automation: G2P systems automate order fulfillment, eliminating the need for manual labor and allowing for faster, more accurate order picking, leading to increased efficiency and productivity.
· Ergonomic and comfortable work environment for pick station operators: By eliminating extraneous walking and allowing operators to stay primarily in place at workstations, goods-to-person systems create a more ergonomic and comfortable work environment, leading to increased performance from the operator.
· Reduced need for storage space: With GTP systems, automation reduces the need for storage space by eliminating the need for aisles and walkways. These systems also take advantage of storing pickable products vertically, sometimes more than 30’, and not just at ground level.
· Improved accuracy by reducing the risk of mistakes in data entry: Goods-to-person systems reduce the possibility of errors in data entry by automating the process, eliminating manual labor, and using advanced technologies such as RFID to ensure correctness.
· Tailored to specific needs and employ various technologies such as robotics, vision systems, and RFID technology: Goods-to-person systems can be tailored to specific needs and utilize a range of technologies, including robotics, vision systems, and RFID technology to improve efficiency, accuracy, and overall performance.
· Fewer labor hours, allowing for more efficient use of resources: GTP systems reduce labor hours, allowing for more systematic use of resources, which can lead to cost savings and increased productivity.
· Reduced need for additional staffing, resulting in cost savings for employee wages and benefits: With fewer labor hours needed, goods-to-person systems can reduce the need for additional staffing, leading to cost savings for employee wages and benefits.
· Elimination of manual movement of items: G2P systems eliminate the need for manual movement of items through workers walking the warehouse, reducing the risk of accidents, injuries, and mistakes.
· Improved accuracy through the detection of inaccuracies in order fulfillment: With the use of advanced technologies such as vision systems and RFID, goods-to-person systems can detect inaccuracies in order fulfillment, allowing for quick correction before shipment.
· Alerting workers to mistakes before an order is shipped out: G2P systems can alert workers to mistakes in order fulfillment before an order is shipped out, leading to improved precision and customer satisfaction.
· Increased customer satisfaction levels: GTP systems improve reliability, efficiency, and overall performance, leading to increased customer satisfaction levels.
· Streamlined order fulfillment processes: By automating the order fulfillment process, goods-to-person systems streamline workflow, reduce errors, and save time and resources.
Types of Goods to Person Systems
Grid Based
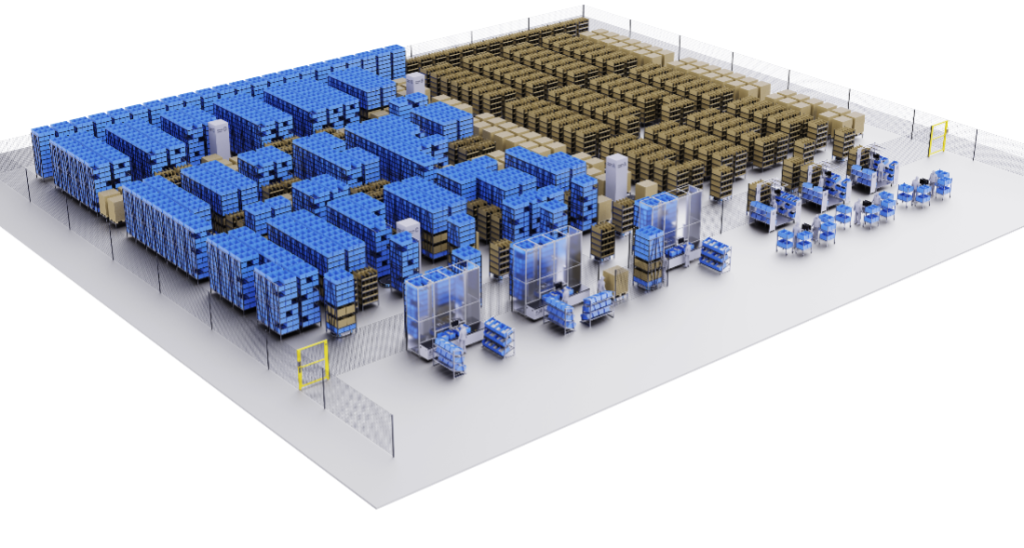
Grid-based systems use a grid of storage locations to house products, typically retrieved with a robotic solution carrying the rack or pallet to the pick station, and then returning to an available location. These solutions can be used to store and retrieve a variety of items, including parts, components, finished products, and raw materials. These solutions don’t require precision racking to be installed, and as a result, typically have short lead times compared to shuttles and other storage solutions.
Since these robots bring an entire rack or pallet of product to the pick station, they are often presenting multiple SKUs to the picker. This can allow for slotting optimization, making the system more efficient. For example, if a customer typically buys batteries or a charger with a power tool, those SKUs can be stored on the same shelf. This way, when the common order of a drill and charger is placed a single robot movement can account for both lines in the order.
While these systems don’t support the vertical storage efficiency of other configurations they typically aren’t limited to standard totes and weight limits around 50lb. They are also more flexible and easier to expand since they don’t require precision racking and in-rack fire suppression.
Shuttles
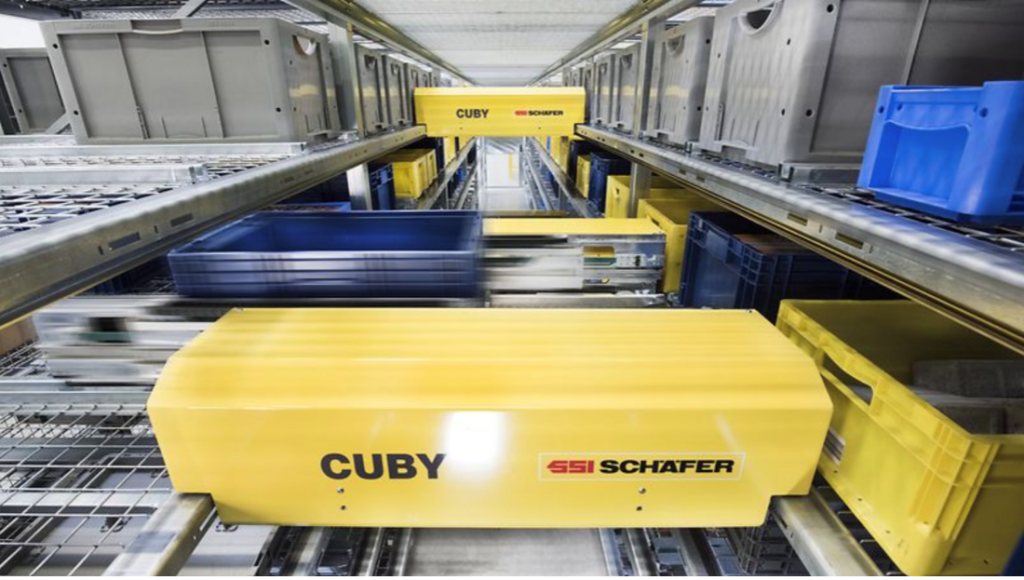
Shuttles work within a GTP system by retrieving the required tote that contains the item in need of being picked. The totes then get delivered to a worker. The inventory is then returned to storage and the next item is retrieved. Due to the rigid infrastructure of shuttles, they are capable of very high speeds and throughputs. Shuttles generally accel in high throughput applications in excess of 5000 lines an hour and when the active SKU count is relatively low (less than 2000).
Robotic G2P with Fixed Rack Storage
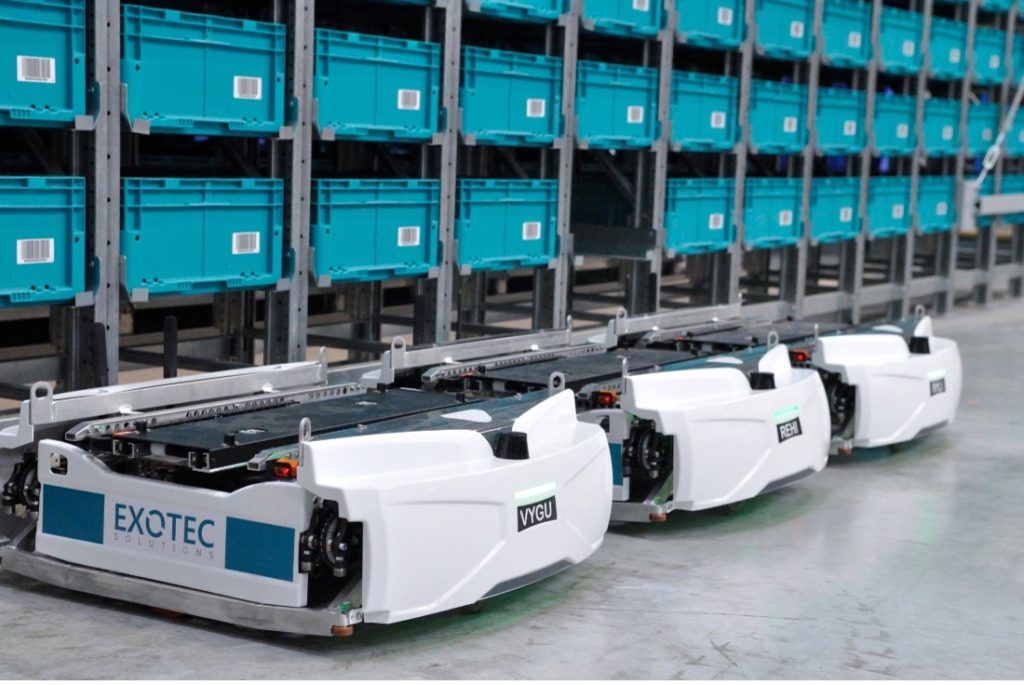
There are a variety of Robotic based G2P solutions that have emerged in the market over the last 5 years. One major differentiator is the structure of the storage.
Some systems, like Exotec and Hai Robotics, require fixed racking to be designed and installed. This racking structure is the basis for the active storage area where the robots retrieve products. It allows for storage over 30’ high depending on the equipment and as a result is an incredibly structured use of warehouse space. These solutions are typically advantageous in situations where the active SKU counts are more than 2000.
Carousel
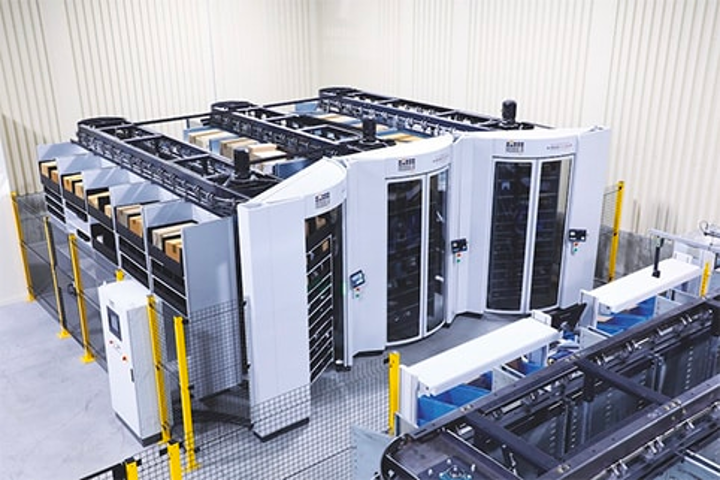
Carousel-based solutions use a series of rotating shelves to store and retrieve items from totes. These solutions can be used to store and retrieve a variety of items, including parts, components, finished products, and raw materials. Carousels are well-suited for applications requiring multiple retrieval points close to them. They can also store and retrieve items in small batches, making them well-suited for order-picking applications.
The main benefit of carousel-based systems is that they can help to improve productivity while reducing errors that can happen with material handling. Carousels are particularly cost-effective for operations with lower throughput and lower skew count compared to other operations.
Goods to Person vs Person to Goods
GTP picking systems are an efficient and cost-effective way of fulfilling orders within a warehouse environment. They involve the robotic selection of goods, which are delivered directly to human workers who package them for shipment at various workstations.
In contrast, person-to-goods systems are manual processes that require human workers to move through the warehouse aisles to locate and select the items required for order fulfillment. Both methods have their advantages and disadvantages which need to be considered when considering which one is suitable for a particular application.
Goods-to-person solutions can reduce labor amounts by reducing the amount of time needed to fulfill orders, but they require significant capital expenditure to purchase and install the necessary equipment. Person-to-goods systems are less expensive upfront but require more human labor, potentially resulting in higher long-term costs.
A thorough analysis must be undertaken before deciding on what type of picking system is best suited for an organization’s needs.
Common Applications
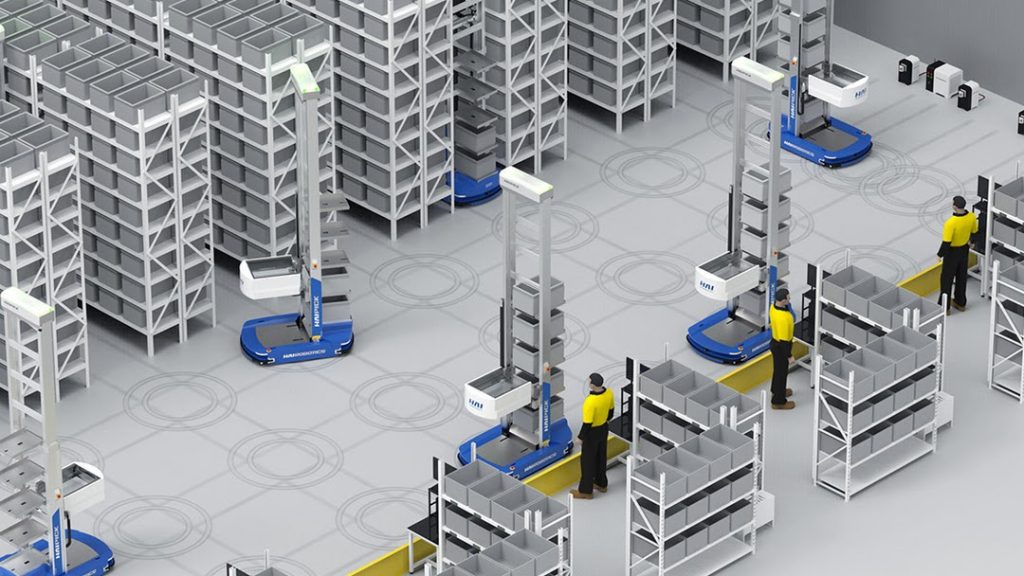
Goods-to-person systems are commonly used in a range of applications, including e-commerce order fulfillment, retail store replenishment, and in manufacturing for spare parts and work-in-progress (WIP) storage.
Imagine an e-commerce warehouse with a goods-to-person system that utilizes robots to automate order-picking processes. In this system, the robots move up and down aisles filled with product bins, picking up the necessary items for each order. When a new order is received, the robots locate the appropriate bins and transport them to a designated workstation. There, a human operator selects the items needed from the bin and places them into a shipping container, which moves along a conveyor belt toward the packaging area. The operator can work quickly and efficiently, as the items are within easy reach and the need to traverse the warehouse is eliminated. The system’s software optimizes the picking order and route, minimizing the amount of time and distance the operator needs to travel between bins.
After the order is completed, the shipping container moves to a packaging location where it is prepared for shipping. The warehouse management system automates and records the entire process, ensuring that each order is fulfilled accurately and efficiently. With a goods-to-person system, the e-commerce warehouse can streamline its order fulfillment process and increase productivity. The robots eliminate the need for workers to traverse long distances, reducing the amount of time needed to complete each order. Plus, the system’s software optimizes the picking order and route, further reducing time and labor.
In retail stores, GTP solutions can be used to automate replenishment tasks that are traditionally done by manual labor. Automated robots can retrieve items from shelves or backroom storage areas and deliver them directly to stocking personnel. This increases efficiency by reducing the time it takes for stockers to locate and fill items on shelves. Additionally, these solutions can help improve inventory accuracy as they reduce human errors associated with manual replenishment processes.
These automated picking systems have also been adopted in manufacturing operations where they are used to assemble components into finished products or subassemblies. By automating this process, manufacturers can reduce production times while improving product quality and reducing costs associated with labor and material handling.
Goods-to-Person System Example
An example of a goods-to-person system that Hy-Tek integrated is with Ariat International.
Company Background
Ariat International is a footwear, apparel, and accessories brand for equestrian sports and other outdoor work and activities. The company has made great strides in footwear since its launch in 1993.
Similar to other industries and companies, the COVID-19 pandemic exposed the lack of flexibility in its fulfillment operations; The Pandemic drastically changed the company’s order profiles and thus its fulfillment needs.
While Ariat is headquartered in Union City, California, the 1 million-square-foot distribution and fulfillment center is in Fort Worth, Texas.
Challenge
The existing facility was set up to process retail store fulfillment with large order profiles. However, COVID-19 accelerated e-commerce growth, increasing the need to change the fulfillment processes.
Solution
Hy-Tek implemented a robotic order fulfillment solution that could handle a wide variety of order profiles.
Results
A flexible and scalable solution that increases picking rates for e-commerce and retail orders.
How to Measure the ROI of Your System?
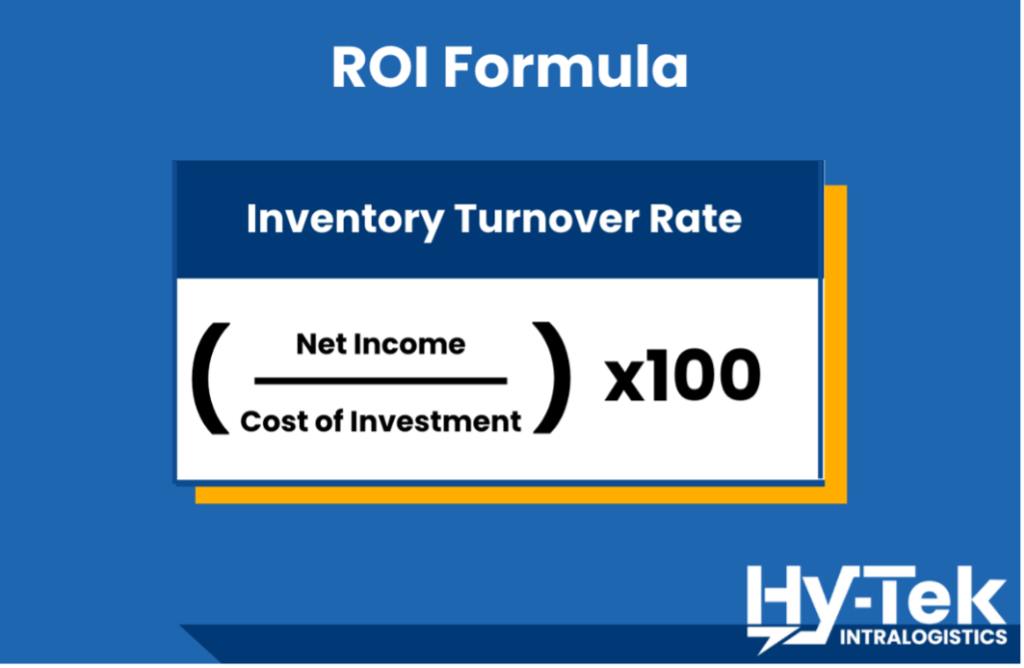
Return on Investment (ROI) is a major factor in determining the success of goods-to-person picking systems. When evaluating the ROI of such systems, it is important to consider both the benefits and costs associated with implementation.
Benefits may include cost savings or increased productivity and revenue, while these fees could include initial investment, training, maintenance, and disruption to existing operations.
To measure the ROI of goods-to-person picking systems, one must compare expected benefits with estimated costs. This can be done by creating a detailed financial model that includes all factors related to implementation and operation.
The results of this analysis should provide clear insight into the potential return on investment for investing in such technologies. It is also important to note that there are intangible benefits that should be considered when evaluating an investment in a goods-to-person system, such as improved employee morale or customer satisfaction.
Conclusion
The potential of goods-to-person picking systems is clear within the supply chain space. This technology can revolutionize the traditional picking process, increasing efficiency and productivity while reducing mistakes.
Moreover, these systems have the capacity to be implemented in a wide range of industries, from manufacturing to e-commerce, providing a variety of benefits for businesses and customers alike.
As such, GTP solutions offer an innovative solution with significant potential for improving operational efficiency across a variety of industries, to help meet increasing customer demand.
It is evident that goods-to-person picking systems are an invaluable asset for many businesses looking to improve their operational efficiency. With proven capabilities and potential for widespread application, these systems present an attractive opportunity for any organization looking to streamline its operations in a cost-effective manner.