Inaccurate inventory can have a significant impact on a business’s bottom line. A study published by the ECR Community Shrinkage & On-shelf Availability Group found that improved stock accuracy boosts sales by roughly 4% to 8%.
Low inventory accuracy is often a result of human error, but this inaccuracy can be mitigated by implementing the proper procedures and systems (WMS, ERP). If you want your business to improve its efficiency and bottom line, you must learn how to calculate inventory accuracy so that you can track your progress over time and have a positive impact on other important warehouse KPIs.
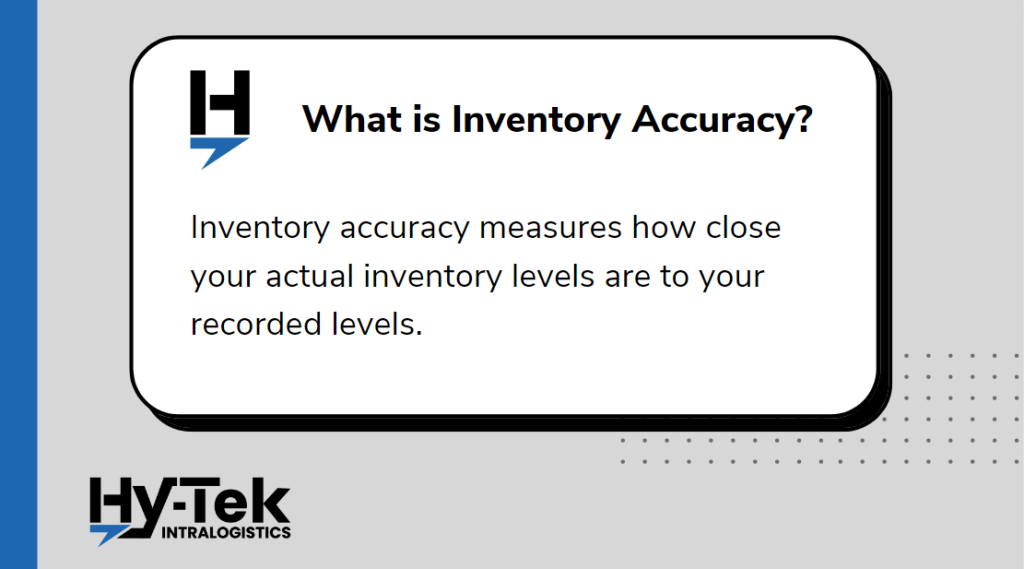
What is Inventory Accuracy?
Inventory accuracy is the accuracy to which the actual quantities of raw materials and finished goods match what systems like ERP says is there. Furthermore, inventory accuracy also factors in whether the material is actually where the systems say it is.
Without an accurate read on inventory, a companyās ability to achieve optimal efficiencies, reduce errors and reduce labor requirements is severely limited and often compromised. You may end up sending pickers to the wrong locations, which results in wasted time and labor costs.Ā Inaccurate inventory data increases backorders which in turn increases overall fulfillment and transportation costs.Ā And worst of all, inaccurate inventory data can have a ripple effect that ultimately impacts customer satisfaction.Ā
Letās put this into an example that many can relate to. Say youāre baking a cake in your kitchen.Ā However, you cannot recall where you put several ingredients and must spend additional time looking for them. The same goes for warehouse inventory: by clearly defining where each item goes and having a system in place that reduces errors, you’ll reap the rewards of downstream efficiency, helping you reduce warehouse costs. Ā
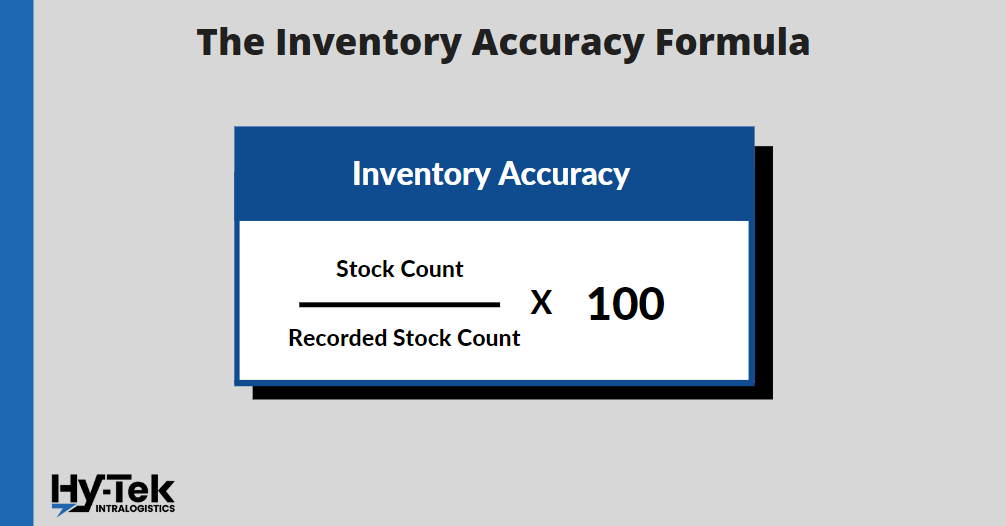
The Inventory Accuracy Formula
To calculate inventory accuracy, you will need to know the quantity of stock that exists and the quantity of stock that is recorded. You can then use the following formula to determine the accuracy percentage:
Stock count / Recorded stock count * 100
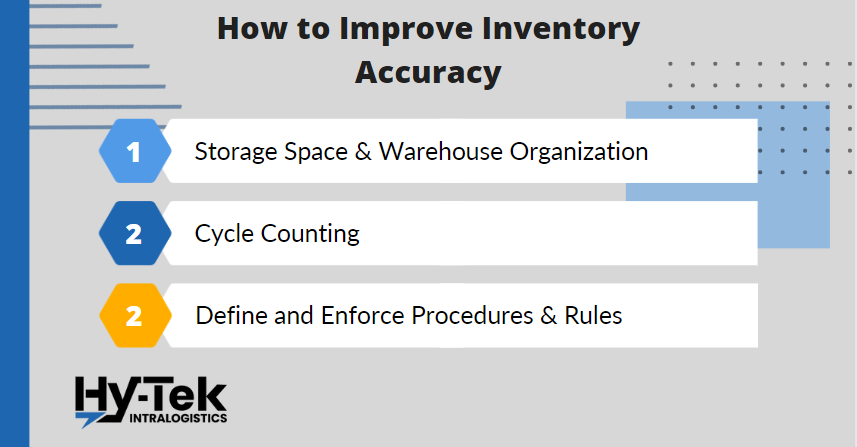
How do you Improve Inventory Accuracy?
Most companies struggle with inventory accuracy. It’s a difficult task to get a good read of what you have in stock.
Having the correct procedures and systems in place can minimize the time and effort needed to increase your inventory accuracy. Let’s take a closer look at how to do that.
Storage Space and Warehouse Organization
If your warehouse is cluttered and cramped, it will be difficult to keep track of what you have on hand. This can lead to stock-outs, overages, and other accuracy issues.
Creating additional storage and inventory space can help to alleviate these problems. Systems can also help with inventory slotting, system-directed put-away, better consolidation, and stock rotation to better utilize your current space and drive up other key warehouse KPI metrics.
When items are correctly stored and easy to access, it becomes much simpler to count and track them. In addition, ample space allows you to store items in an orderly fashion, making it easier to locate them when needed.
As a result, increasing your storage and inventory space can lead to greater accuracy.
Cycle Counting
Cycle counting is a method of inventory control that allows you to count small sections of your inventory on a regular basis, rather than conducting one large annual count.
However, where some go wrong is they use it as a method to track and repair mistakes merely. Instead, it should be used to confirm that errors don’t occur again by following the chain of events back to its origin and creating a new standard operating procedure to guarantee the error isn’t repeated.
This can improve your accuracy in a number of ways.
- It can help you stay on top of your inventory levels on a more regular basis, so you are less likely to run into stock-outs.
- It will help you identify any issues with your counting procedures before they cause major problems.
- You’ll have greater control over your inventory levels since any mistakes will be detected and fixed considerably faster.
A warehouse management system (WMS) can make a huge difference in your cycle counting process and drive proactive behavior instead of reactive behavior. The system can generate daily counts by using real-time data to immediately notify someone when a mispick occurs. This notification can show up in several ways (email, mobile device alert, read report) so that a task can be created to have someone go and cycle count where the error occurred.
Define and Enforce Procedures and Rules
The effectiveness of the warehouse is only as good as its documented policies and procedures.
It’s critical to define all the processes in the warehouse, especially when it comes to effective inventory movement and precise data recording.
The policies and procedures should be released to employees formally through training, and they should be tested on the material to make sure they understand it. If noncompliance issues arise, corrective action should be taken immediately.
If employees regularly deviate from the documented process, the process should be reexamined.
A WMS is not just a tool to help users; it is designed to take the focus off of them and let the system do the work. The implementation team takes the time to understand how the system works and implements processes within it to remove human errors, improve onboarding, and make it more intuitive. Then it comes down to continuous improvement within the system to continue improving inventory accuracy.
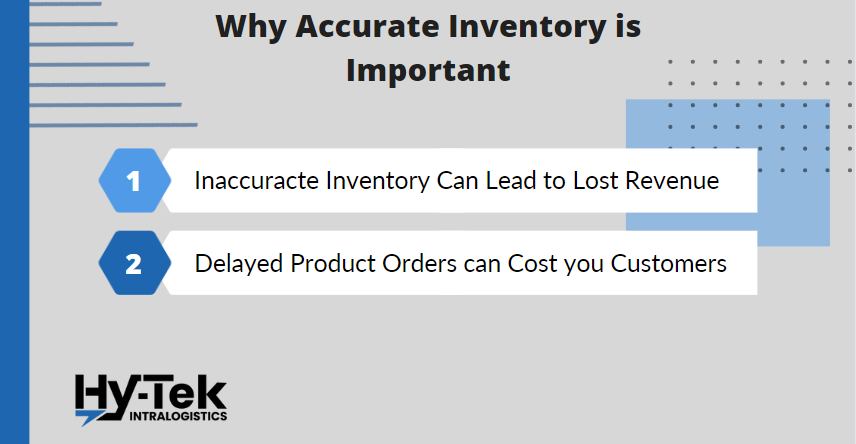
Why is Accurate Inventory Important?
Inventory accuracy is key to minimizing delivery delays and keeping customers happy.
By having records that accurately reflect what you have on hand, you’re able to operate more efficiently and meet customer demand.
As a cherry on top, accurate inventory means you’re not overstocking or understocking, which minimizes wasted resources.
Let’s take a closer look below at some specific reasons why it is crucial to have an accurate inventory.
Inaccurate Inventory Can Lead to Lost Revenue
Inaccurate inventory levels can lead to missed sales and excess stock, both of which have serious consequences for your business.
It’s therefore important to have accurate inventory levels so that you can stay on top of your reorders and ensure that you have enough time between lead times to receive items for incoming orders.
This is crucial for maintaining a positive customer experience and avoiding lost business.
Delayed Product Orders can Cost you Customers
If you’re running out of stock, you’re losing customers. A study from Voxware found that 69% of customers are less likely to buy from you again if their order is not delivered within two days of the promised delivery date.
To make matters worse, if you’re constantly running out of stock, your customers are likely to go to your competitors to find the products they need. Zendesk found that 80% of consumers said they would switch to a competitor after more than one bad experience.
This all boils down to the Amazon effect. Customers expect to receive their exact order within an extremely short period (1-2 days). Speed and accuracy is more critical now than it has ever been.
FAQ
What is a good inventory accuracy rate?Ā
The answer to this question depends on several factors, such as the industry you’re in, the type of products you sell, and the size of your inventory. WERC put together research that found a good inventory accuracy rate to be 99%, and best-in-class (the top 20% of companies) to be 99.888%Ā
What is the average inventory accuracy?Ā
A great inventory accuracy rate is 99%, which is the goal that many businesses aspire to achieve. Maintaining this level of accuracy can be difficult, but it is worth the effort as it can help improve your bottom line.Ā
There are several receiving practices to help you get there. Here are a few:Ā
⢠Inspect your order against the items on the shipping notice to make sure you got everything you ordered. If not, let the vendor know ASAP!Ā
⢠Make sure all items received are in acceptable condition before putting them on the shelves.Ā
⢠Utilize barcode scanning to speed up the receiving process and provide real-time dock-to-stock time.Ā
⢠WMS! A WMS focuses on the organization and optimization of storing and tracking inventory from receiving to shipping.Ā