What is Flexible Automation?
Flexible automation refers to systems and technologies that can adapt to fluctuating requirements such as order volumes, labor shortages, space optimization, or any other business requirement that may change.
In terms of warehousing and distribution, flexible automation systems are designed to enhance efficiency, productivity, and responsiveness in warehousing operations while accommodating dynamic business needs.
They enable warehouses to handle diverse products, fluctuating order volumes, and evolving customer demands with greater ease and agility.
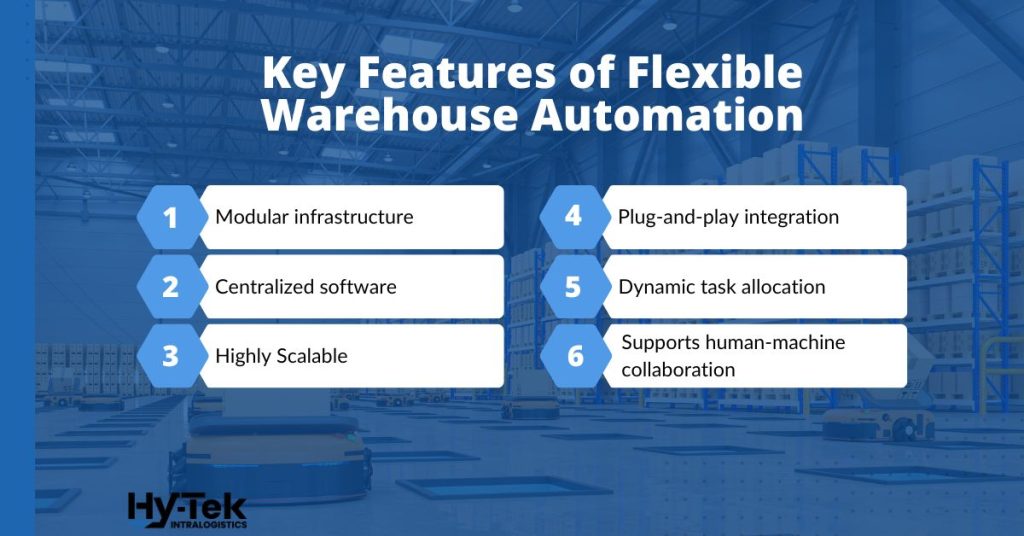
Here are some key aspects of flexible automation in warehousing:
- Modular Equipment: Flexible automation relies on modular equipment that can be easily configured or combined to perform different tasks.
- Software Control: Centralized software provides the flexibility to modify and adapt processes without significant reprogramming or reconfiguration.
- Scalability: Flexible automation systems are scalable, allowing warehouses to adjust their automation capabilities as needed. Whether the warehouse needs to accommodate seasonal fluctuations or business growth, the automation infrastructure can be easily expanded or contracted to match the demand.
- Plug-and-Play Integration: Components within a flexible automation system are designed for easy integration and interchangeability. They often follow standard protocols and interfaces, allowing new equipment or technologies to be seamlessly integrated into the existing system. This plug-and-play capability simplifies the process of incorporating new material handling systems.
- Dynamic Task Allocation: Flexible automation enables dynamic task allocation based on real-time data and changing priorities. For example, automated systems can be programmed to adjust their workflow based on order volume, order urgency, or inventory availability. This adaptability improves efficiency and reduces bottlenecks.
- Human-Machine Collaboration: Flexible automation doesn’t necessarily replace human workers but focuses on collaboration between humans and machines. By automating repetitive and physically demanding tasks, workers can focus on more complex or value-added activities. Human operators oversee the automation system, perform supervisory roles, and handle exceptions or unusual situations.
Overall, flexible automation in warehousing empowers businesses to adapt to changing market conditions, improve operational efficiency, reduce costs, and enhance customer satisfaction. It enables warehouses to achieve higher levels of responsiveness, agility, and productivity while maintaining the ability to quickly adjust to evolving demands.
Fixed vs Flexible Automation
Fixed automation refers to automation systems that are more difficult to adapt. Flexible automation is designed to easily adapt and expand for peak season or as the company grows. Flexible automation allows you to add storage and robots quickly and easily.
However, flexibility is subjective and takes different shapes and sizes. It is not just about being able to expand or change a system but also about the ease of doing so. The effort required to make changes or adapt the system should be cost-effective and minimize disruption to operations.
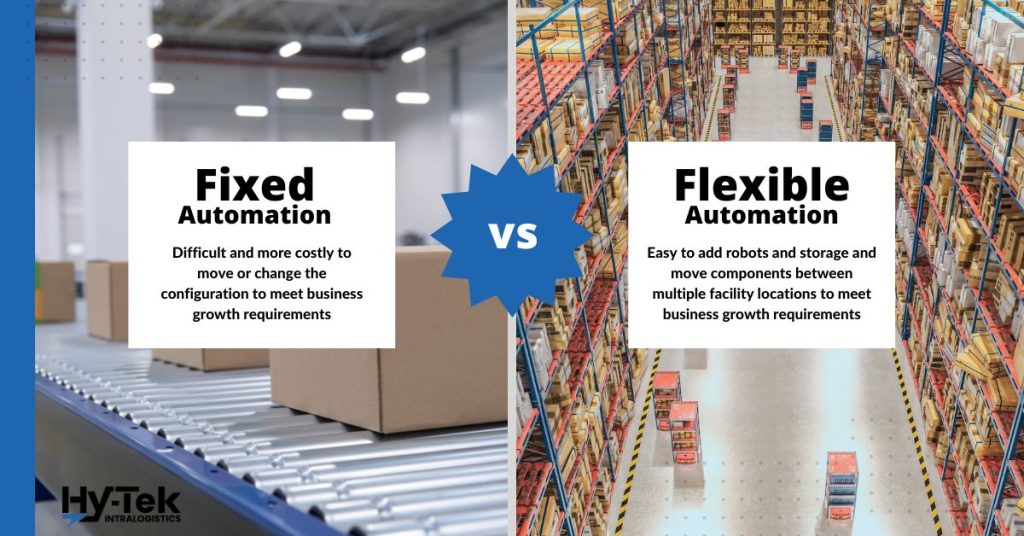
The key concept of flexibility in automation is the ease of change – the easier it is to change or adapt the system, the more flexible it becomes. This is important because change is inevitable in any industry, and the easier it is to manage change, the better for everyone involved.
Challenges that Flexible Automation Solves
Implementing flexible automation in a warehouse aims to address several challenges and improve overall operations. Here are some common challenges that can be mitigated through flexible automation, especially in terms of storage:
- Fluctuating Order Volumes
- Changing Product Mix
- Labor Shortages
- Order Fulfillment Speed
- Seasonal Demand Peaks
- Space Optimization
- Adaptability to Technological Advances
How to Identify Flexible Automation
In today’s ever-changing business landscape, companies must be flexible and adaptable to stay ahead of the curve.
“Plug and play” technology has components that can be easily added or removed to expand the system as needed. This approach helps companies to drive through peak and average volumes and adjust to different time frames, whether it’s a single time period of the year or the time period of the month.
One critical aspect of this is finding solutions that can expand on a larger scale with minimal or no downtime to operations.
1. Assess Change Management
When considering flexible technology, it’s important to think about the change management involved.
For example, if our volume spikes by 30%, how do we respond? Do we add more aisles, more grids, deploy more robots, or rely on labor? Each option has its own ease, difficulty, and cost.
When prioritizing flexibility and adaptability, automation should be the answer, allowing for scalability and quick adjustments in days or weeks instead of months or years.
In the past, we would throw more people at the problem during peak times. The goal was to get the product out of the building. Nowadays, we strive for a “plug and play” approach, where integrators, like Hy-Tek, have components that can be easily added or expanded to handle peak and average volumes.
We can flex the system up or down based on different time periods or specific industry needs using robotic technology.
Aside from the mechanical considerations, there’s also a commercial aspect to think about. Is your solution provider open to concepts like as-a-service pricing or equipment rental options?
These are new ideas in advanced automation and goods-to-person space, which traditionally operated under a capital expenditure (CapEx) model. However, with the introduction of more flexible technologies, we can now explore different pricing models to better serve our partners and clients.
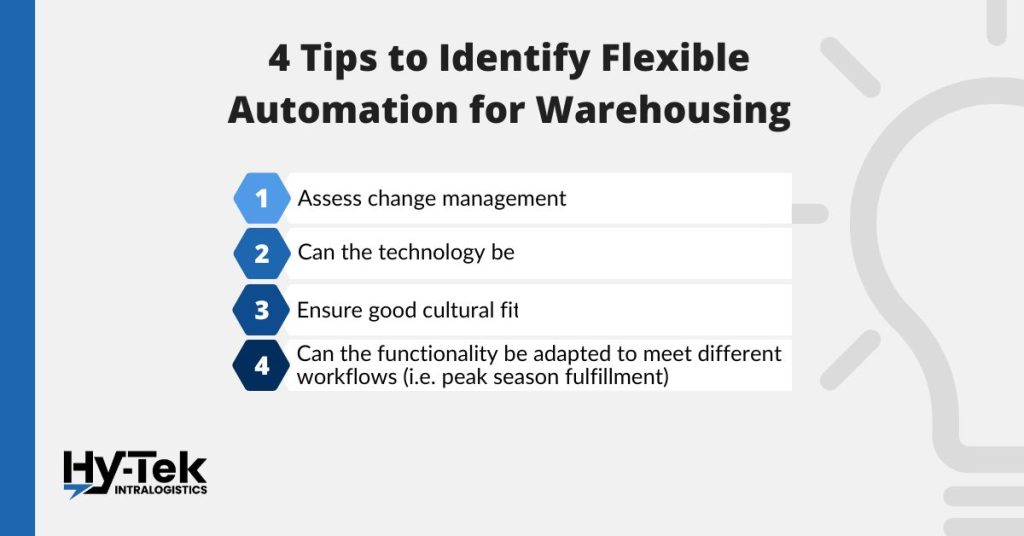
2. Can the technology be used across facilities?
As companies grow and expand their networks, they need to be able to move their technology and solutions from building to building, or even from city to city, in order to remain efficient and effective. This is one of the biggest challenges.
However, companies are working to create templates or platforms that can be used across their entire network, allowing them to move robotics and solutions wherever they are needed.
In addition to the challenges posed by retail, companies also deal with a lack of available labor. In the past, companies could manage uncertainty with labor, but that is no longer the case. As a result, companies are looking for opportunities to consolidate, reposition, move, relocate, and expand in order to navigate the labor shortage.
Flexible technology is a key part of this strategy. Companies with rigid infrastructure that cannot be moved or adjusted are at a disadvantage. However, companies with flexible technology can pick up their automation and move it from one facility to another, expanding their opportunities for expansion and consolidation.
3. Ensure a Good Cultural Fit
In today’s world, where the market demands flexibility, businesses must adapt to survive. And to do that, they need their employees to be happy and productive. However, the warehousing industry, in particular, has some of the highest turnover rates in the country, making it challenging to keep employees for extended periods.
That’s where flexible automation systems come into play. They take the burden of change away from the employee and allow for better workload distribution. For instance, during Black Friday, when companies need to work double shifts, flexible automation makes it possible to plan work schedules effectively, removing uncertainty from employees’ daily lives.
Investing in automation and turning warehouses into a competitive advantage shows a company’s commitment to its employees, which trickles down to all levels of the business. And companies that have invested in automation have seen a significant increase in employee feedback surveys. This is because automated environments are less physically stressful, which makes employees happier and more productive.
4. Can the functionality be adapted to meet different workflows?
Adjusting to the different picking processes and requirements that may accompany peak season is a crucial aspect of flexible automation. Can the automation handle different types of items, such as totes and cases? Can it utilize existing infrastructure without significant facility upgrades? By having fewer limitations, operations become more adaptable and adjustable.
An example illustrates the importance of flexibility. In a tote-based goods-to-person system, a customer faced difficulties during peak seasons due to their full case handling operations. The lack of flexibility in the automation prevented them from optimizing their operations. However, with more flexible automation, they could have easily adapted to changing needs and saved resources.
Working With an Integrator to Identify Flexible Automation
In the realm of flexibility, it’s sometimes challenging to quantify the ROI. However, the value becomes evident when we delve into thought exercises and ask the right questions. By exploring different scenarios and understanding the nuances, we realize the tangible benefits that flexibility brings.
Flexibility is not only about expanding or reconfiguring systems but also about offering entry-level options. A system that starts with a few robots can grow and expand throughout the entire facility, allowing for incremental implementation and training. This flexibility in entry-level solutions promotes wider adoption of robotic technologies in various industries.
An experienced robotic integrator like Hy-Tek Intralogistics can help you identify and asses flexible automation systems.
By embracing the conversations and exploring the subjectivity surrounding flexibility, we gain a deeper understanding of its value and its ability to address the challenges and opportunities that businesses face.