Your distribution center is the backbone of your supply chain, and reducing costs within it can significantly impact your overall efficiency and profitability. You can streamline your operations and increase profitability by identifying and eliminating unnecessary waste.
In this blog, we’ll explore some of the best methods for reducing warehouse costs in 2023, including implementing different types of automation, utilizing software, optimizing inventory management, and implementing a strategic approach to shipping and transportation.
Whether you’re looking to cut costs at an existing warehouse or planning to construct a new one, these strategies will help you save money and stay ahead of the competition. It’s time to get serious about reducing warehouse costs, and we’re here to show you how.
Ways to Reduce Warehouse Costs
- Implement a WMS
- Use Just-In-Time Inventory Management
- Optimize Picking Processes
- Introduce Warehouse Automation Technology
- Upgrade Barcode Scanners and RFID
- Define Operating Procedures
- Implement Vertical Storage Solutions
- Implement Cross-Docking
- Use Preventative Maintenance Programs
- Retain Employees
1. Implement a Warehouse Management System (WMS) to streamline operations and improve efficiency
A WMS is your secret weapon for streamlining operations and boosting efficiency. It’s a software system that increases efficiency by automating the management of warehouse activities such as receiving, putaway, picking, packing, and shipping.
With real-time visibility into inventory and activity, manual tracking errors and misaligned inventory are eliminated, saving time and money from stockouts and overstocking. That means your warehouse personnel can work faster and smarter, resulting in faster turnaround times, better reorder decisions, lower stockout costs, and fewer errors.
Businesses that already possess a WMS that is older and lacking in capabilities may consider adding a Warehouse Execution System (WES), which can compensate for a WMS that is not adequately optimizing material handling system usage, namely underutilization or large peaks and valleys. A WES—which acts as the go-between of a facility’s WMS and Warehouse Control System (WCS)—can be integrated with any WMS and can improve efficiency by optimizing order execution, control automation, managing congestion, and optimizing workflows.
2. Reduce costs with Just-In-Time Inventory Management
Just-in-time (JIT) inventory management is a powerful tool for cutting costs and aligning production and delivery with actual demand. The goal of JIT is to minimize the amount of inventory on hand while ensuring that the necessary materials and products are always available when you need them.
This approach is ideal for companies that operate in fast-paced, highly competitive markets where customer demand can be challenging to predict. With JIT, you’ll reduce excess inventory and storage costs and stay nimble to meet customer needs.
One of the essential principles of JIT is pull systems: where actual customer orders rather than forecasts trigger production and delivery. Pull systems ensure that inventory is only produced and delivered when needed, reducing the risk of excess inventory and storage costs.
Another fundamental principle of JIT is frequent, small deliveries, which reduce the risk of stockouts and improve the flow of materials and products through the warehouse while reducing safety stock. With JIT, you’ll be able to respond quickly to changes in demand and keep your costs under control.
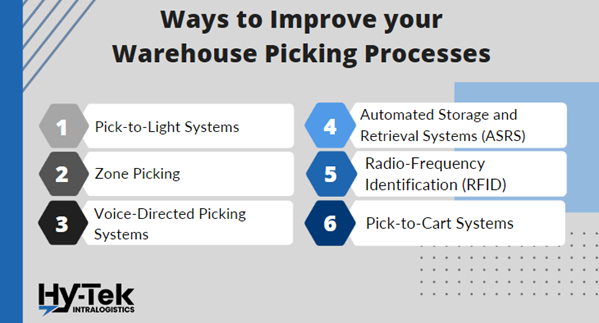
3. Reduce Travel Time by Optimizing Picking Processes
One key aspect of optimizing picking processes is reducing the travel time between picks, which can be achieved through various strategies.
- Pick-to-Light Systems: These systems use lights and displays to guide pickers to the exact location of each item, which increases the speed of the picking process by reducing manual searching.
- Zone Picking: The warehouse is divided into different zones, and pickers are assigned to specific zones, reducing the need for travel between different warehouse areas.
- Voice-Directed Picking Systems: Voice recognition technology guides pickers through the picking process. This can reduce the time and errors associated with picking by reducing the need to look up items manually.
- Automated Storage and Retrieval Systems (ASRS): These systems use automated robots to store and retrieve items in the warehouse.
- Radio-Frequency Identification (RFID): RFID technology uses radio waves to communicate between a reader and a tag attached to an item. This allows for automated tracking of items in the warehouse without manual scanning.
- Pick-to-Cart Systems: In a pick-to-cart system, pickers are equipped with mobile carts with RFID readers or other technology. The pickers use the carts to scan or identify items as they are picked, reducing the need for manual item tracking and increasing the speed of the picking process.
An important note: Reducing travel time between picks can significantly impact warehouse efficiency, but it is not the only consideration when optimizing picking processes. Some other factors that should also be considered include the number of picks per hour, the accuracy of the picking process, and the overall cost of the system.
4. Reduce labor costs with warehouse automation technology
By automating repetitive and time-consuming tasks, warehouse automation technology can significantly reduce the need for manual labor and improve overall warehouse efficiency. This can be achieved through a variety of different technologies, including WMS, WES, automated storage and retrieval systems (ASRS), robotic pick arms, and AMRs.
Warehouse automation technology is a highly effective solution for reducing labor costs because it can replace repetitive and time-consuming tasks, such as picking and packing, the movement of materials, and data entry.
5. Use barcode scanners and RFID technology to improve accuracy and reduce errors
Manual processes such as inventory tracking, order fulfillment, and shipping become more efficient and accurate when using barcode scanners and RFID tags.
When done manually, workers scan each item’s barcode as it is picked, packed, or shipped, sending the information to a WMS for inventory updates and order status tracking. This eliminates manual data entry, reducing errors.
Similarly, RFID tags placed on each item in the warehouse are scanned by RFID readers and transmitted to the WMS for real-time inventory tracking and improved accuracy. RFID also confirms that the correct items have been picked, reducing human error in order fulfillment.
However, manual scanning and tag placement can still be time-consuming and labor-intensive. To further streamline the process, upgrading to print and apply, in-motion labeling, and slotting automation can remove repetitive tasks and save on labor costs. These technologies automate the printing and placement of labels, as well as the movement and organization of inventory within the warehouse, leading to even greater accuracy and efficiency.
6. Optimize warehouse labor with defined operating procedures
In manufacturing and fulfillment, time is money—the more efficient the process, the lower the cost. Standard operating procedures help to eliminate waste and improve efficiency.
By establishing clear protocols for each task, businesses can minimize errors and wasted time, leading to cost savings.
Clear protocols for each task will minimize errors and time spent, while standard work instructions, continuous improvement processes, and implementing KPIs will provide a framework for measuring performance and identifying areas of improvement.
7. Utilize floor space effectively by implementing vertical storage solutions
Vertical storage solutions include multi-level shelving, mezzanine floors, and vertical carousels. These solutions can increase the storage space available in a warehouse without the need to expand the physical footprint of the facility.
One of the main benefits of vertical storage solutions is that they can maximize the use of available space. This can be particularly important in warehouses operating at capacity or struggling to accommodate growing inventory levels. By using vertical space, businesses can store more items in the same footprint, reducing the need for additional storage facilities.
8. Implement cross-docking to eliminate the need for long-term storage
Cross docking is a logistics technique in which goods are transferred directly from incoming trailers to outgoing trailers with minimal or no storage in between.
Because the items are going directly from a truck to another supply chain link, there is no need for storage space. By eliminating the need for long-term storage, businesses can free up valuable warehouse space for other uses, such as production or distribution. This can reduce the costs associated with leasing or maintaining warehouse space.
Cross-docking also allows for the rapid movement of goods through the warehouse, reducing the time and labor required to access inventory. This can improve productivity and reduce labor costs.
9. Implement a preventive maintenance (PM) program to reduce equipment downtime and repair costs
Preventive maintenance refers to regularly inspecting and servicing equipment to identify and fix potential issues before they become significant problems.
A business can improve productivity and save money by implementing a PM program that reduces equipment downtime.
10. Focus on Employee Retention
Did you know that replacing an employee can cost up to twice their annual salary?
That is why having a solid strategy for retaining top-performing employees and repositioning some of your underperforming employees is crucial.
You can keep employees engaged and motivated by offering competitive pay and benefits, opportunities for growth, and fostering a positive work-life balance. Regular feedback and open communication also help to address any issues, keeping employee turnover low.
FAQ
How can warehouses save money?
Warehouses can save money by eliminating unnecessary steps and touches. A streamlined process saves you money by looking at current processes to find where you may be duplicating or retracing steps.
What are the 4 basic functions in a warehouse?
The 4 basic functions in a warehouse are storage, material handling, packing and shipping, and inventory control.
How can I make my warehouse more profitable?
You can make your warehouse more profitable by making it as simple as possible for workers to locate items. This will increase warehouse efficiency, improve customer order times, lower labor costs, and boost profits.