A lights out warehouse is a type of automated warehouse that uses robotics and other advanced technologies to operate with little or no human intervention.
This can increase productivity and efficiency in the supply chain, while also providing other benefits such as reduced labor costs, improved safety, and increased accuracy.
Benefits of a Lights Out Warehouse
There are several benefits of lights out warehouses, including increased productivity and efficiency, space savings, reduced labor costs, improved safety, and increased accuracy.
1. Increased Productivity and Efficiency
One of the biggest benefits of a lights out warehouse is that it can increase productivity and efficiency in the supply chain. This is because automated systems can operate around the clock, which means that orders can be fulfilled faster and more accurately.
2. Space Savings
Automated warehouses often have higher storage density than traditional warehouses, which means that more products can be stored in a smaller space.
3. Reduced Labor Costs
Another benefit of lights out warehouses is that they can help to reduce labor costs. This is because automated systems can often do the work of several people, and in an economy where manual labor is hard to find, automation is extremely helpful to maintaining and scaling fulfillment operations.
In addition, lights out warehouses often have lower employee turnover rates than traditional warehouses, which can further reduce labor costs.
4. Improved Safety
Lights out warehouses can also be safer than traditional warehouses, as there are fewer humans working in them. This means that there is less chance of accidents occurring, and it also reduces the chances of theft and other crimes taking place.
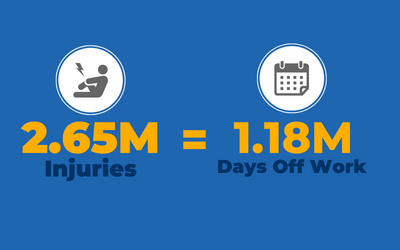
According the Bureau of Labor Statistics, in 2020, there were 2.65 Million recordable injury cases, totaling 1.18M days away from work. These costs are astronomical for employers.
5. Increased Accuracy
Lights out warehouses can also be more accurate than traditional warehouses. This is because automated systems can pick and pack orders more accurately than people can. Hence, it is less likely that errors will be made, and it also means that customers are more likely to receive their orders on time.
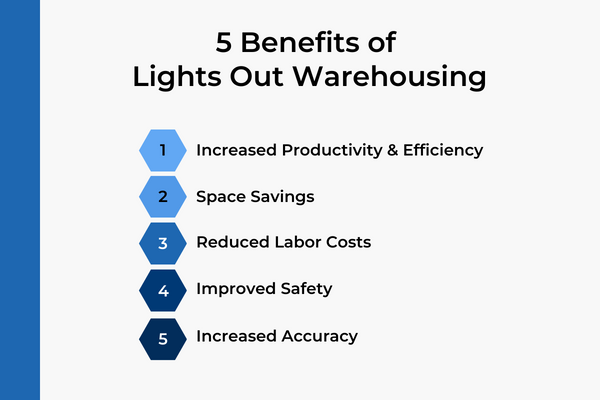
History of Material Handling Automation
The history of warehouse automation began in the early 1900s with the introduction of conveyor belts. These were initially used to move heavy objects from one place to another, but soon they were used to transport smaller items as well.
In the 1950s, material handling automation began to be used more extensively in warehouses. This was driven by the increasing use of assembly lines in manufacturing, which required parts and products to be moved quickly and efficiently from one place to another.
Now, warehouses and fulfillment operations are designed to operate with minimal human intervention, and it used a variety of advanced technologies such as conveyor belts, robots, and sensors.
An account by Dave Tavel, Senior Vice President of Sales at Hy-Tek Intralogistics.
“Forty-two years ago, I started working for a very large consumer-goods manufacturer, and I clearly remember sitting in a meeting and discussing “lights out manufacturing”. The concept of a lights out manufacturing facility was evolving, and processes to achieve this were gradually improving. As the development in technology became more sophisticated, the ability to manufacture complex items without human intervention eventually became common practice.
A couple of years later I entered the world of material handling. Consultants and very progressive companies launched initiatives to define and create “lights out” for the fulfillment and distribution sector to benefit in the same manner as the manufacturing industry. That was in the late ‘70s and early ‘80s, and even at the turn of the millennium, the question remained, ‘Would it be possible to process work in distribution facilities without people, and have a true lights out distribution facility?'”
Examples of Lights Out Warehouse Technologies
There are several technologies and robotics that can be used in lights out warehousing.
The majority of technology is based around the picking process since this task accounts for a large portion of labor-associated costs.
Automating this task has driven labor out of the pick process by eliminating waste such as walking, and we are now addressing the other aspect of the pick process by automating the task-time related to selecting the appropriate item.
Advancements are also being made regarding automated trailer unloading and loading. On-demand packing is driving efficiencies in numerous ways but ultimately eliminating the need for human intervention. The evolution of goods-to-person to goods-to-robot, usage of autonomous mobile robots (AMR), huge gains in vision technology and warehouse software, as well as AI and deep learning has all spawned out of the search for lights out.
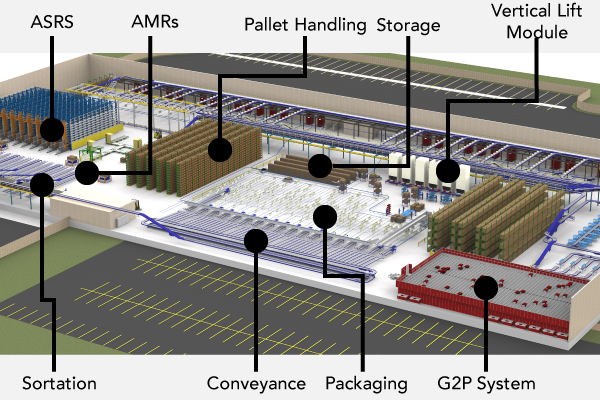
Conveyor Systems
Another system that can be used in lights out warehousing is a conveyor. Conveyance systems are used to move products around the warehouse, and they can be used to connect different technologies throughout the warehouse.
Sortation
Sortation automation in warehousing includes automated sifting, categorizing, separating, dividing and distribution tasks.
Packaging
Robots can easily and securely pack items with the highest precision. Packaging automation consists of in-line labeling and weighing, auto-bagging machines, corrugate machines for auto-boxing, and more.
Autonomous Mobile Robots (AMRs) and Automated Guided Vehicles (AGVs).
AMRs and AGVs can move pallets and other material around the facility. This allows for human-free moving of pallets. They are able to handle all load sizes and mixed case palletizing. There are pros and cons to each technology, but here’s the main difference between AMRs and AGVs.
Automated Storage and Retrieval Systems (AS/RS)
An automated storage and retrieval system (AS/RS) is a type of lights out warehouse technology that is used to automatically store and retrieve products.
AS/RS systems usually consist of a storage area, a retrieval area, and a conveyor system that connects the two. The storage area is typically made up of shelves or racks, and the retrieval area is usually a loading dock where orders are picked and packed.
Goods-to-Robot
Goods-to-Robot technology is a type of ASRS and an advanced version of Goods-to-Person that utilizes mobile robots to retrieve items and bring them to a stationary pick station. At the pick station, a robot (versus a human) picks the items.
Exotec and Caja are examples of goods-to-person technologies that eliminate travel time to inventory pick locations, thus increasing pick-speed and reducing labor costs.
Challenges of a Lights Out Warehouse
While we have developed the technology and created automation for specific areas within a facility, the key to all of this is centered around integration.
What does that mean? Metaphorically, it means taking the individual, automated puzzle pieces and fitting them together to form a completed puzzle, giving you a clear image. The ultimate end game is to make sure that each automated piece within a facility compliments and interfaces appropriately with each other thus forming a cohesive, automated solution.
Despite tremendous gains in technology, we have not completely solved the puzzle. This is due, in part, to many factors including day-to-day operations, capital requirements, technology advancements, environmental and cultural change, etcetera.
The question remains, “Are we at a point where we can truly accomplish a lights out distribution facility or warehouse?”
In reality, plans do not always go as expected. These complex technologies consist of electro-mechanical components that are assembled into a working system which requires maintenance. This poses a challenge because self-repairing equipment does not currently exist (to our knowledge).
Lights out distribution facilities are rigid, and they like consistency. In fulfillment, things change rapidly on a day-to-day and season-to-season basis. With such rapid changes, human intervention is often required to perform tasks such as training robots or updating software.
All of these challenges need to be considered when thinking about the practicality of achieving a facility with lights out automation.
What kinds of facilities benefit the most from lights out technology?
There are several types of warehouses and fulfillment centers that can benefit from automation, including those that:
1. Fulfill high-volume products.
If you sell a high volume of products, then automating your warehouse can help you to keep up with customer demand. This is because automated systems can pick and pack orders faster than people can and can operate 24/7, which means that you will be able to fulfill more orders in a shorter period of time.
2. Need to optimize space.
If you have a large storage area, then automating your warehouse can help you to utilize it more effectively. This is because automated systems can often store more products in a smaller space than people can, which means that you will be able to use your storage space more efficiently. In addition, automating your warehouse can also help you to reduce labor costs, as you will need fewer employees to run your operation.
3. Struggle to find and retain workers.
If you find it difficult to find and retain workers, then automating your warehouse can help you to overcome this challenge. This is because automated systems do not get tired and do not need breaks, which means that they can work for longer periods of time than people can. In addition, automated systems do not require health insurance or other benefits, which can further reduce your labor costs.
4. Have non-ideal working conditions.
If there are ergonomic concerns associated with the manual tasks such as lifting heavy objects or high-repetition of movement that could pose injury, then automating these tasks can alleviate this concern.
5. Process similarly-sized products.
Lights out automation is easiest for facilities that fulfill a large number of similarly-sized items.
Warehouses that process standard sizes of processed food, packs of canned or bottled soda, makeup, clothing, or shoes for example, can make use of automated work.
Implementing An Automated Facility and Achieving Lights Out
It starts with data, accurate forecasts, and a detailed understanding of what the result needs to satisfy. Cohesive solutions require definitive criteria that define the “why?”, and without it, we should not even start the effort.
The adage of “bad data in – bad result” is significantly more important in the search for a lights out warehouse. Simply put, automation is not flexible when trying to eliminate all humans from the equation, which ironically, is the intended purpose of automation. Therefore, the data and forecasts MUST be correct going in. Here are the Warehouse KPI Metrics that you should be tracking.
Once the data has been analyzed, and the design criteria has been established, it is imperative that an agreement is reached, top to bottom, within the organization that is undertaking the effort. Engage the design team, and review in detail the expectations of the effort.
The next step is to develop the functional requirements document in which the overall effort will be defined. Upon completion, another round of approvals must be achieved. The effort will fail if buy-in and complete understanding is unclear.
In summary, the desire to achieve lights out manufacturing has revolutionized the way we view production and the movement of goods. In turn, the quest to achieve lights out automation has benefitted the distribution and fulfillment sectors of the supply chain. It will continue to drive lower costs, faster response times, and higher accuracy rates which will benefit both the seller/distributor and customer.
The question of pursuing a lights out distribution facility is an individual choice. It comes with risk, but, with the help of an experienced integrator to successfully implement, great reward