the world of warehousing, efficiency and accuracy are not just buzzwords, they are survival mechanisms. One pivotal process that marries these two critical components is ‘Order Picking’.
This article will guide you through the basics of order picking, different methods of order picking, factors to consider when choosing a method, and the role of technology in modern order picking.
- Understanding the Basics of Order Picking
- Elements of Picking an Order
- Pros & Cons of Each Order Picking Method
- Importance of Efficient Order Picking
- Factors to Consider
- Implementing Picking Technology
Understanding the Basics of Order Picking
Order picking is an integral part of warehouse activities, making up as much as 55% of the operating expenses. Thus, an efficiency made in the order picking process has the potential to greatly affect the efficiency of the entire facility operation. The key is to optimize order-picking efficiencies while maintaining the highest level of customer satisfaction.
What is Order Picking?
Order picking is the selection of items from stock in a warehouse to fulfill customer orders. In other words, order picking involves picking the right product, in the correct quantity, at the right time for dispatch.
There are many elements to order picking and it is a complex process that requires careful planning and execution. It involves several steps, such as receiving customer orders, locating and picking appropriate items, and preparing them for shipment.
The Picking Process
When an order is received, items and quantities should systematically be validated against current inventory levels to ensure the complete order is available. This may entail maintaining a good level of data integrity, but it can provide huge efficiencies to the warehouse order-picking process.
Once the order is dropped for processing, the next step is to systematically assign the pick from locations. This is typically done by a warehouse management system (WMS) or warehouse execution system (WES).
The key factors at this stage of the order-picking process are order-pick accuracy at optimal throughput rates.
The final stages of the order-picking process involve preparing orders for shipment. This may include order packaging, labeling, and loading for delivery.
Elements of Picking an Order
There are many elements to picking an order, and the combination that you utilize will play a large role in the efficiency and accuracy of your order fulfillment process.
The order picking process consists of these 5 elements:

- Release Policy: how orders are organized and distributed to picking operators
- Picking Strategy: how picking operators collect and organize items
- Picking Structure: the physical layout of the picking areas
- Picking Method: the systems or technology that the picking operators utilize
- Picking Techniques: ways picking operators achieve the picking strategy. For example, a cluster cart holds multiple discrete orders where each order has a specific tote. Pick & pass refers to discrete orders that utilize a zone structure.
For example, discrete picking can also utilize cluster picking or zone picking with a pick and pass technique.
Each method has its pros and cons depending on the size of the facility, type of products being picked, and customer orders. Knowing which order pick strategy works best for a particular warehouse can help minimize errors, reduce costs, and improve order fulfillment times.
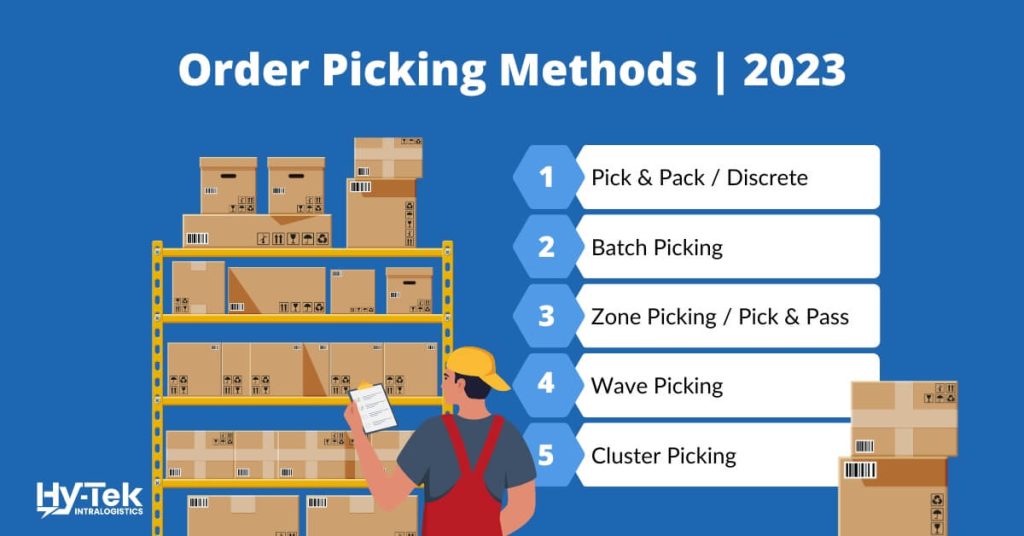
Pros & Cons of Each Order Picking Method
When it comes to order picking in a warehouse, there are several methods, techniques, and tools you can utilize.
It’s important to note that the following methods, techniques, and strategies are not independent of each other – rather, any order-picking solution should seek the optimal combination of methods, techniques, and strategies.
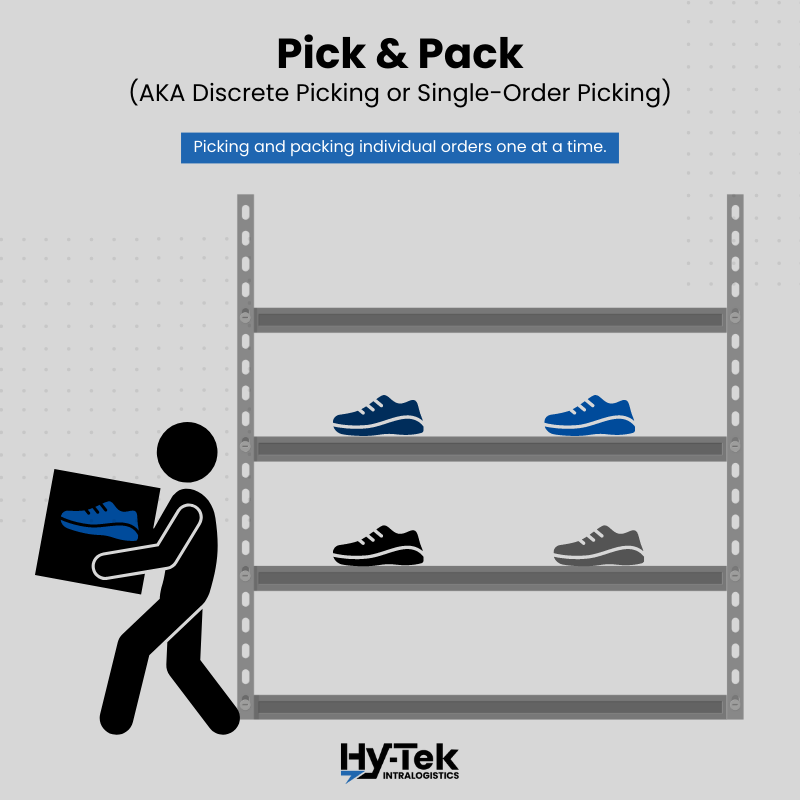
Pick and Pack (Discrete Picking or Single-Order Picking)
This method involves picking and packing individual orders, one at a time. It typically works well for businesses with a small number of orders (e.g., a retail fulfillment warehouse servicing 40 stores a day) Discrete picking allows for a high level of customization and accuracy in fulfilling customer orders.
Pros:
- Ease of implementation
- Order picker accuracy and performance are easily tracked
Potential Cons:
- Time-consuming
- Labor-intensive
- Excessive picker travel
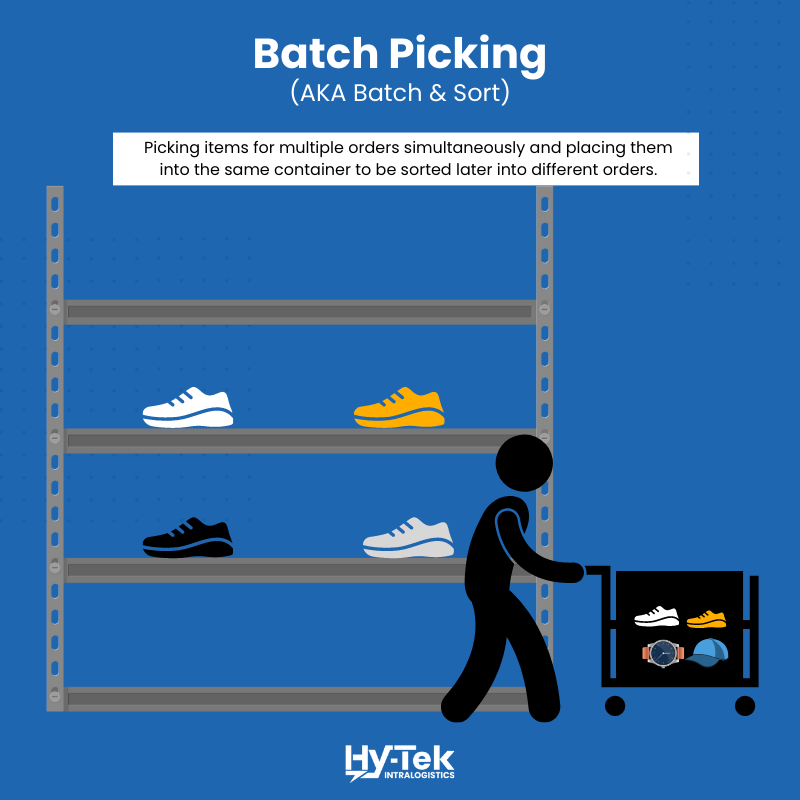
Batch-Order Picking
Another method commonly used in warehouses is batch picking (sometimes called batch and sort). This method involves picking items for multiple orders simultaneously. Typically, operations with a large number of smaller quantity orders are advantaged with this picking strategy. Batch picking is often more efficient than single-order picking because it consolidates picking routes and reduces travel time within the warehouse.
Pros:
- Enables faster order fulfillment for a high volume of orders.
- Reduces order picker travel.
Cons:
- Product sortation and order consolidation is needed for multi-unit orders.
Zone Picking (Pick and Pass)
Zone picking is a method that divides the warehouse into different zones, with each picker assigned to a specific zone. Each picker is responsible for picking items only from their designated zone. There are two common types of zone picking:
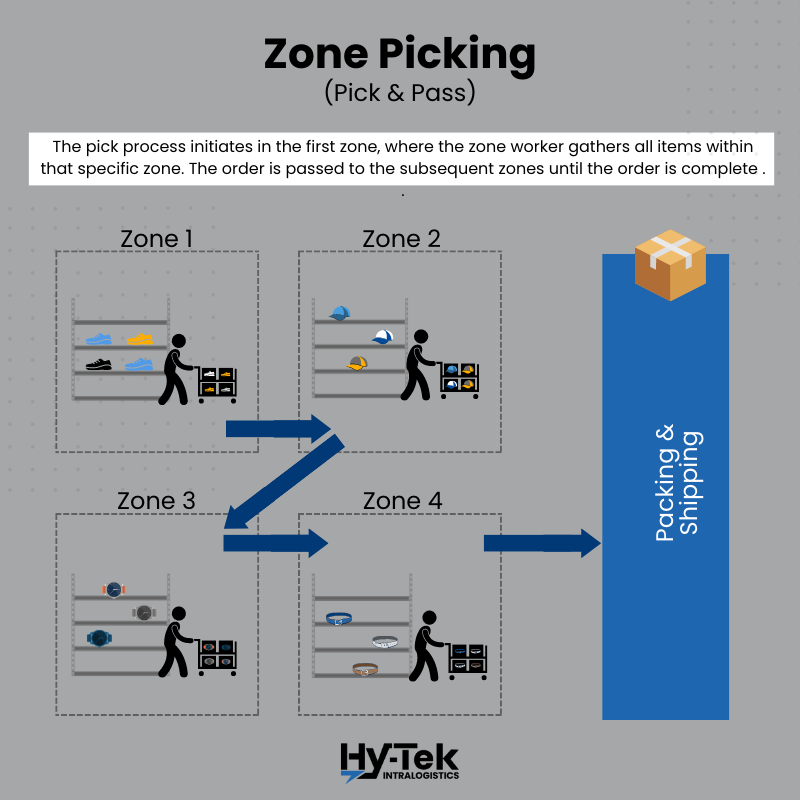
Pick and Pass Zone Picking
In a pick-and-pass zone-picking method, an order is passed from zone to zone where workers in each zone place items into the order tote. Once the tote makes it through the last zone, it is sent to packing.
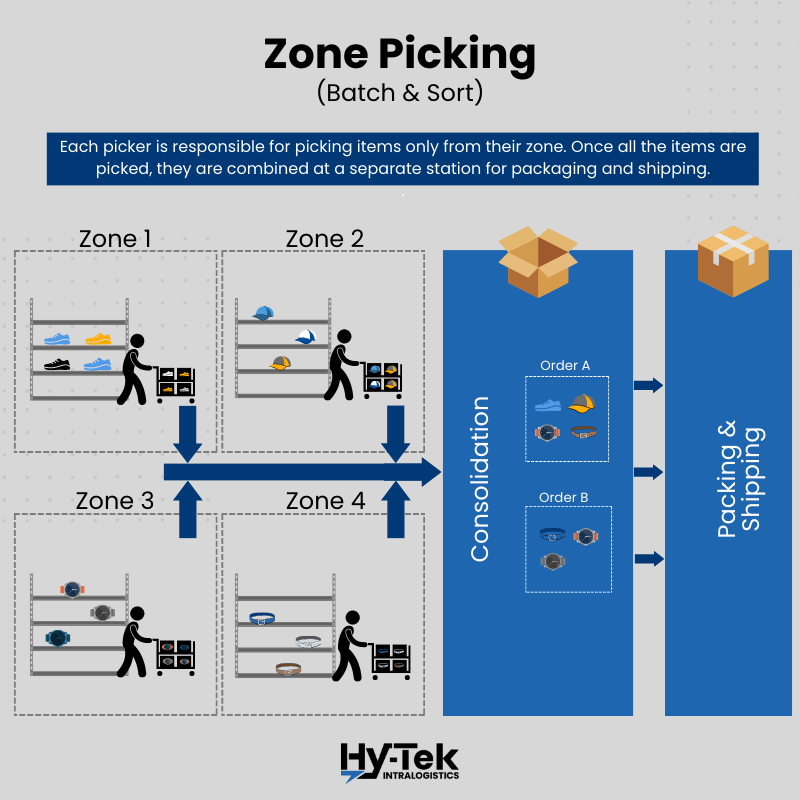
Batch & Sort Zone Picking
In a batch-and-sort zone-picking method, workers in each zone pick items for multiple orders. Once all the items are picked from each zone, they are combined at a separate station for packaging and shipping.
This method helps reduce congestion in the warehouse and increases order-picking speed. By assigning specific zones to each picker, it minimizes the travel distance and time required to pick items. Zone picking is particularly effective in large warehouses with a wide range of products and a high number of orders to fulfill.
Pros:
- Slot items by SKU velocity more efficiently
- Reduce aisle congestion
Cons:
- Since orders will consist of items picked from multiple zones, the products will need to be consolidated.
- Some zones may experience more activity than others, creating unequal workloads. This can be evened out with a zone-balancing strategy.
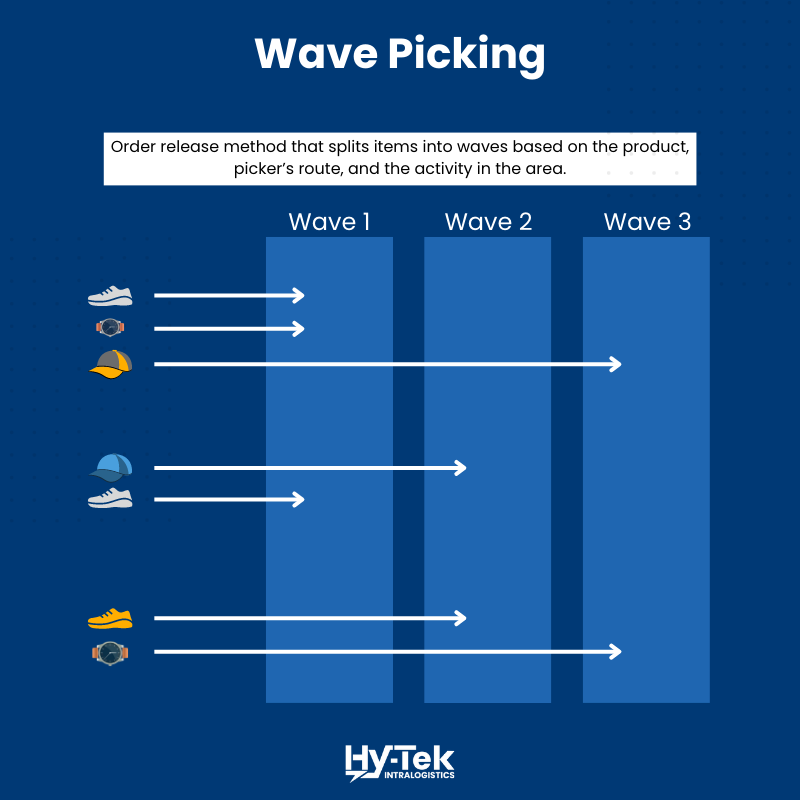
Wave Picking
Wave picking might be best described as an order release method rather than a picking method. A “wave” describes how orders are given to order pickers and it can be utilized in conjunction with batch picking and/or zone picking.
With wave picking, orders are grouped together based on specific criteria and assigned to pickers accordingly.
Pros:
- Efficient organization and planning of order release
- Ability to forecast labor demand
Cons:
- Not all waves disperse work equally, causing some pickers to wait for work to be released
The continuous wave-picking method allows for new orders to be transferred to the current workload (current wave) dynamically based on picker location and workload. This method does require sophisticated software for precise order timing.
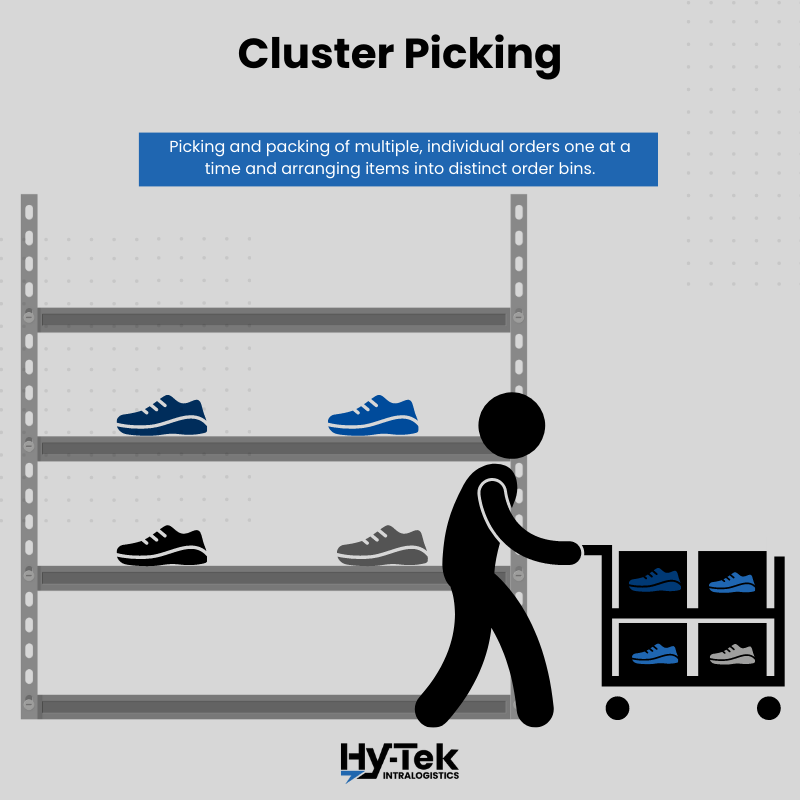
Cluster Picking
Cluster picking simply means that multiple discrete orders are picked simultaneously. It is similar to batch picking, however, cluster picking involves arranging items into distinct bins. This strategy allows workers to fulfill multiple orders in a single trip while alleviating the need for further sortation.
Pros:
- Minimizes touches and the need to sort downstream
- Works for small- to medium-sized items
Cons:
- Limited number of orders per cart per trip
- Long pick path for slower-moving items (less popular)
- Not ideal for large items (cannot fit on cart)
Overall, the choice of order-picking method depends on the specific needs and requirements of the warehouse. Whether it’s piece picking, batch picking, zone picking, or wave picking, each method offers its own advantages in terms of efficiency, accuracy, and speed. By selecting the most suitable methods, warehouses can optimize their order fulfillment process and provide excellent service to their customers.
Importance of Efficient Order Picking
An efficient facility is one that maximizes productivity while minimizing expenses. Optimizing the order-picking process is a great way to help gain an efficient system. Increasing productivity while reducing order error helps not only reduce facility expenses but also improve customer satisfaction (a key to maintaining and growing future business).
Furthermore, efficient order picking reduces the likelihood of errors and mistakes in orders. When items are picked accurately and with validation checks, there is a lower chance of shipping the wrong products or quantities to customers. This not only saves costs associated with returns and replacements but also enhances the reputation of the warehouse as a reliable and trustworthy supplier.
Factors to Consider When Choosing an Order Picking Method
Choosing an appropriate picking method should be based on several factors such as warehouse size, product nature, and order volume. Let’s delve into these factors:
Warehouse Size and Layout
Warehouse size significantly affects the order-picking process. Larger warehouses may benefit from zone or wave picking to make optimal use of resources. The layout must also be considered, as the arrangement of products can affect picking efficiency.
Nature of the Products
The type of products stored also influences the picking method. For instance, perishable items or those requiring special handling may involve specific picking procedures.
Volume of Orders
The volume of orders processed also plays a crucial role. Warehouses with high order volumes might lean toward methods like batch or wave picking, which can handle large numbers of orders simultaneously with greater efficiency.
Implementing Technology in Order Picking
Advances in technology continue to revolutionize warehouse operations. Here’s how both low- and high-level picking technology fits into the mix:
Use of Barcodes and Scanners
Barcodes and scanners have greatly improved order-picking accuracy and speed. Errors have been drastically reduced, and real-time tracking has streamlined warehouse management.
Automated Order Picking Systems
Automated picking systems including pick-to-light, or voice-directed picking, and vision picking systems have reduced manual labor, boosted productivity, and improved accuracy in various warehousing operations.
The Role of Robotics And Software in Order Picking
Robotics, such as goods-to-person technologies and autonomous mobile robots, are becoming increasingly common in warehouses. These automated helpers work around the clock, reducing errors and increasing productivity. They also decrease the physical workload on human workers, leading to a safer work environment.
To achieve synchrony between robotic systems and have better inventory control, labor management, and real-time visibility – you can utilize a robust software. A dedicated picking software can be used to increase accuracy and customer satisfaction!
In conclusion, effective and efficient order picking is critical to warehouse operations. It pays to invest attention and resources into choosing and implementing the right order picking methods. Embracing technology can also yield significant benefits. In the competitive world of warehousing, every pick counts.