My college professor always said in class; you don’t know what you don’t know. At the time, as a college student, that saying was completely lost on me.
Fast forward to today, I have seen the wisdom of that idiom play out time and time again with the businesses and warehouse operations we have helped.
The power of information, especially business intelligence in these digital days, cannot be understated. Being able to access weekly, daily, and up-to-the-minute data has a dramatic impact on warehouse operations – keep reading to find out how.
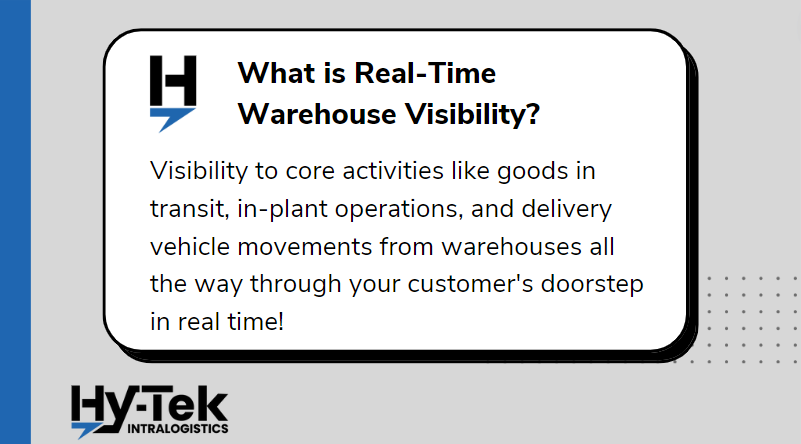
What is Real-Time Warehouse Visibility?
In today’s world, businesses need to be able to see all aspects of the movement of goods throughout the entire supply chain, from manufacturing to delivery at customer endpoints.
Supply chain visibility refers to tracking core activities like goods in transit, in-plant operations, and delivery vehicle movements from warehouses all the way through your customer’s doorstep in real time!
In traditional systems, however, it can be difficult when you don’t have access or cannot sync certain pieces that make up the supply chain management puzzle. For example, when third-party logistics providers, transport management systems (TMS), and warehouse management systems (WMS) don’t communicate with each other very well, it becomes difficult to track down information about inventory or shipments.
With real-time visibility in your warehouse and supply chain operations, on the other hand, you can easily stay up to date on every aspect of product movement, reduce shipping delays and inventory shortages, optimize your workforce for efficiency, and save money on shipping costs.
The Challenging Nature of Supply Chain Visibility
The supply chain is a complex web of organizations and systems that must work together to ensure products make it to their destination. However, getting the different departments and organizations to work well together can be challenging because, as said by Victor Coronado, “Information in most organizations exists in silos.”
Whether you’re a small business or a Fortune 500 company, disruptions can occur at any point in supply chains. Here are some of the largest challenges for visibility:
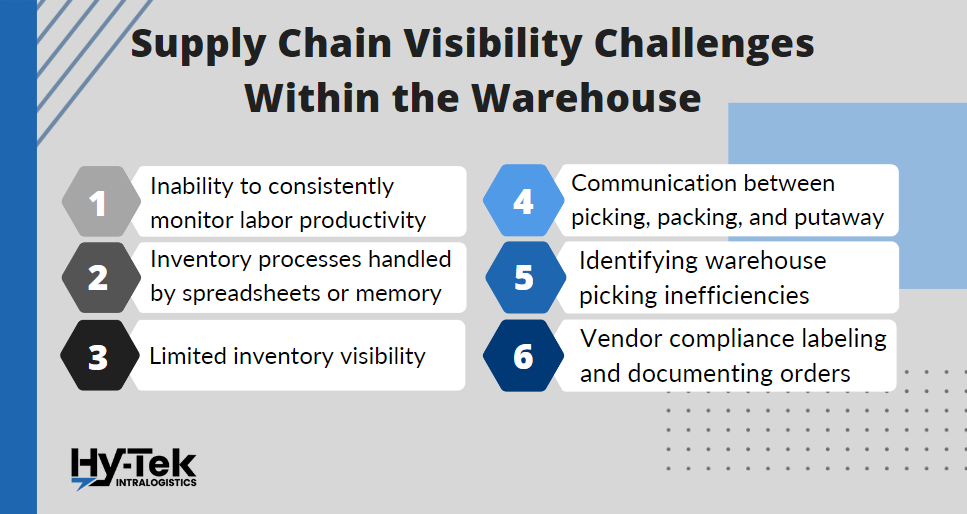
Supply Chain Visibility Challenges Within the Warehouse:
- Inability to consistently monitor warehouse labor productivity
- Handling warehouse inventory processes by spreadsheets or by memory
- Limited inventory visibility
- Communication between picking, packing, and putaway processes
- Warehouse picking inefficiencies are hard to identify
- Vendor compliance with labeling and documentation of orders
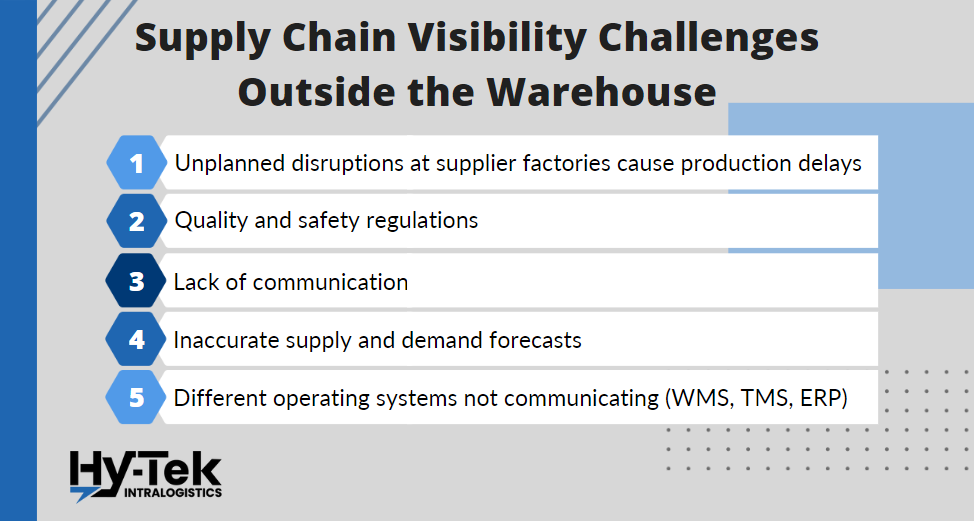
Supply Chain Visibility Challenges Outside the Warehouse:
- Unplanned disruptions at supplier factories cause production delays
- Quality and safety regulations
- Lack of communication between sales and supply chain
- Inaccurate supply and demand forecasts
- Issues getting different operating systems to communicate (WMS, TMS, ERP)
By understanding the challenges of supply chain and transportation visibility, businesses can take steps to mitigate potential disruptions and protect their bottom line.
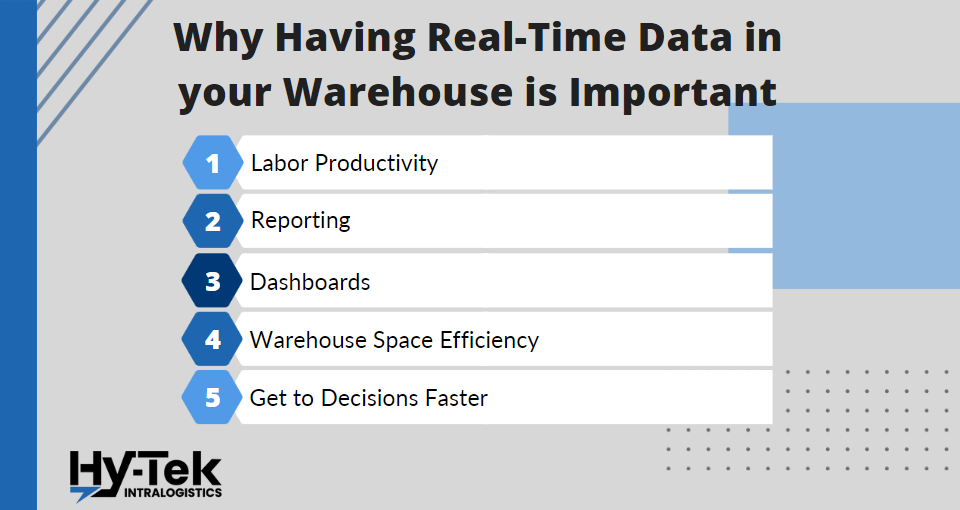
Why Having Real-Time Data in your Warehouse is Important
Real-time data in your warehouse allows for better decision-making, smoother operations, and improved customer experience and satisfaction.
It allows you to track and trace shipments, monitor inventory levels, and utilize machine learning to anticipate any potential delays or issues before they happen. Below are some more specific ways that it helps your business:
1. Labor Productivity
Real-time data can measure labor productivity in receiving, picking, and shipping. Measuring an employee’s number of picks, putaway, accuracy, and average times throughout the week and during their shift can lead to key insights.
Who are your key performers? Who might need more training? Are there any on-floor habits that need to be addressed? This can reveal training needs, employee assignments that take advantage of their talents, or needed action.
2. Reporting
In the past, reporting could be a real task.
Taking multiple reports or spreadsheets and combining them into one document or PowerPoint can take hours, if not days, to produce. Then by the time you send or present the report, the data has already changed.
With Real-Time Data, the WMS can provide general and customized reports that can be automated to run and then emailed or even texted to managers and executives so they can see how the warehouse is performing.
Another key element to this is the data can be presented in a data or visual form with graphs.
3. Dashboards
Over the past few years, if you have walked through any major distribution center, you will see large monitors that display an array of dashboards for the warehouse team to see.
On these dashboards, they could see the progress of receiving inventory or how many picks are left in the shift. These dashboards are used to keep the warehouse staff up to date on their workday and progress.
4. Warehouse Space Efficiency
With real-time data – You can analyze where your slow-moving inventory is being stored and, adversely, where your high-turn products are located. By analyzing and then moving these products to align with picking, you can reduce the time to pick and the total steps taken.
5. Get to Decisions Faster
Armed with the most up-to-date business intelligence, teams can make data-driven decisions and be confident that they are doing what is best for their operations and staff.
You can easily find and make changes as situations occur that could impact warehouse or shipping operations productivity.
Real-World Examples of Real-Time Visibility
What is real-time visibility? Real-time visibility in warehousing refers to the ability to access and monitor up-to-date information about inventory levels, stock movements, and order status as they happen, enabling better decision-making and improved operational efficiency.
Example 1: RepairClinic
RepairClinic relies on a mid-market ERP software package to automate, plan, and track business processes. Adding Hy-Tek’s WMS to the mix provided real-time visibility across the entire warehouse and supply chain. The results were new levels of productivity, accuracy, and cost-savings.
RepairClinic Vice President of Supply Chain put it this way: “People are amazed at the technology driving our distribution center. Adapting to changes in picking, packing, and all other areas has increased productivity while improving quality.”
Today the company is:
- Gaining real-time visibility and reducing bottlenecks by integrating the warehouse management software to MS Dynamics GP
- Operating an integrated and efficient distribution center resulting in a 100% productivity increase
- Streamlining picking and shipping to process over 8,000 orders on peak days with minimized headcount
- Boosting order fulfillment speed and accuracy
- Improving shipping efficiency while controlling related costs
Example 2: ORR Safety
ORR’s nine distribution centers process orders for equipment from more than 600 suppliers. Integrating the ERP system, order fulfillment, inventory, and shipping is critical to streamlining processes, ensuring accuracy, and controlling costs within the supply chain.
Hy-Tek’s integrated solution provided ORR Safety with:
- Annual Freight & Labor cost savings of nearly $500.000
- Seamless Dynamics GP integration
- An integrated environment that doubled annual revenue growth.
- Sustained improvement in order fulfillment speed and accuracy
- Minimal headcount increase
- Real-Time visibility in orders, SKU movements, inventory status, individual/team productivity and other key metrics.
ORR’s Corporate Distribution Manager stated: “[Hy-Tek’s] integrated WMS and shipping solution saves us nearly $500,000 each year in freight and labor costs.”
Example 3: Consumer goods manufacturer
Recently a well-known Midwestern consumer goods manufacturer made the decision to expand distribution to a national scale. Painfully aware of the logistical challenges that come with expansion, the company realized that they had reached the limit of Dynamics GP in this area. Managing these tools, processes, and resources required new levels of control, visibility, and automation. A new WMS solution with MS GP integration was critical to managing growth.
After an extensive search, Hy-Tek’s WMS was selected. Today this company is documenting new levels of control, tracking, and efficiency. Furthermore, the scalability of the WMS is providing just the levels of functionality needed to meet the demands of today while anticipating what lies ahead.
There are a number of other examples of how an integrated WMS/Dynamics GP solution is delivering measurable results:
- 99% + order accuracy
- Year-end inventory virtually eliminated
- 100% Productivity Increase
- Increased Order Processing with lower labor costs
FAQ
What is real-time supply chain visibility?
Real-time supply chain visibility is a process of continuously tracking materials and their progress through every stage of the supply chain journey. This information is displayed on a live dashboard, allowing business owners to quickly identify any issues, whether they are on-site or at a remote location.
What are the significant benefits of real-time visibility in the supply chain?
Real-time supply chain information allows businesses to improve efficiency, reduce waste, and provide better decision-making. This is done by live tracking materials and identifying any issues before they cause serious problems.
How do you achieve end-to-end supply chain visibility?
1. Audit your current supply chain operations and mark areas for improvement
2. Define your ideal process for managing supply chain operations
3. Improve communication tools
4. Invest in more advanced tracking tools and labeling systems
5. Utilize a WMS for reporting
6. Set up KPI’s for consistent measurement
How does supply chain visibility improve the planning process?
When shippers can see their inventory, they can improve customer service with proactive status updates and manage goods in transit, thereby limiting disruptions and mitigating risk.