25.8% said they have installed voice-directed picking, 18.3% use radio frequency identification (RFID), 12% use pick-to-light, and 11.1% have installed automated storage and retrieval systems (AS/RS).
With a heightened focus on improving efficiency and inventory accuracy at every stage of the process – inbound, storage, and outbound – warehouse and distribution center managers are evaluating the effectiveness and efficiency of handheld scanners.
The Role of Handheld Devices in Warehouse Management
Handheld barcode scanners play a vital role in modern warehouses, where they seamlessly integrate with inventory management software or warehouse management system to efficiently track the movement of goods and streamline order-picking activities.
These devices eliminate the inefficiencies and inaccuracies associated with pen and paper-based inventory control.
When goods arrive at the warehouse, each item or case is labeled with a unique barcode. As warehouse personnel handles these items, they use handheld scanning devices equipped with barcode scanners to read the barcode labels or QR codes.
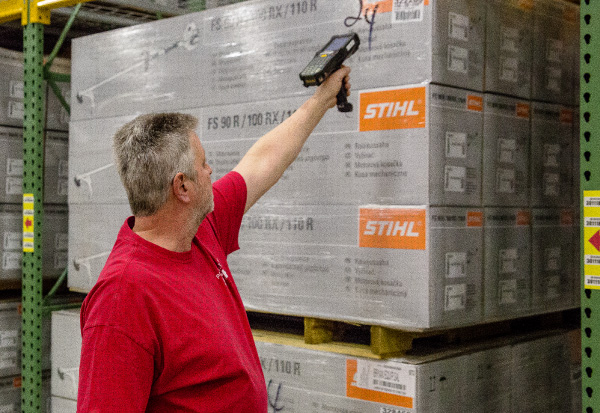
The scanner reads the black and white lines of the barcode, converting the pattern into a numeric or alphanumeric code. This code corresponds to a specific product and is linked to the warehouse’s inventory management system.
As goods are picked, packed, and shipped, the barcode scanners update the system in real-time, ensuring accurate and up-to-date information on inventory levels. This process enables warehouse managers to monitor stock levels efficiently, optimize storage space, and improve order fulfillment accuracy, ultimately enhancing overall warehouse productivity and customer satisfaction.
Types of Warehouse Scanning Devices
The main types of warehouse scanning equipment are:
- RF Devices
- Wearable Devices
- Smartphones & Tablets
- RFID Reader
- Mobile Solutions
Radio Frequency (RF) Devices
One of the most widely used handheld devices in warehousing is the Radio Frequency (RF) device. These rugged barcode scanners are specifically designed for the warehouse environment and are capable of tracking goods throughout their journey, from receipt to putaway, picking, packing, and dispatch. Their durability and reliability make them a popular choice among warehouse operators.
The biggest drawback of using a handheld scanner is that it requires one hand to be occupied while operating the device.
Wearable Devices
Most wearable devices feature a keyboard and a compact monitor worn on the arm, accompanied by a small ring scanner on the hand.
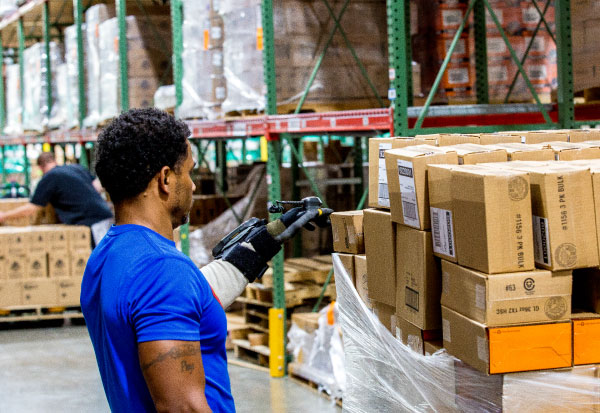
Adopting wearable technology eliminates this inconvenience as there is no need for repetitive holstering and upholstering of the handheld device.
This, in turn, enhances productivity since workers can now use both hands efficiently, leading to faster task completion.
However, it is essential to consider that wearables might be relatively more expensive depending on their make and model.
Smartphones and Tablets
While RF devices are effective, they can be relatively expensive. As a result, many businesses in the distributive trades have turned to consumer-grade smartphones and tablets as an alternative. Smartphones, in particular, have emerged as the most widely used mobile device in supply chain and logistics operations.
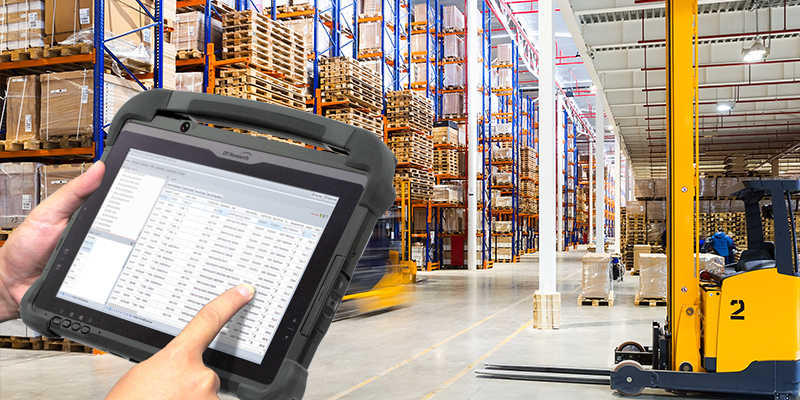
Image Source: DTResearch
Workers are already familiar with smartphones and tablets, making it easier for them to adapt to these devices quickly. The larger screen sizes of tablets and smartphones allow for more visual instructions to be provided to warehouse staff, combining images with text commands for improved clarity and accuracy.
Additionally, there are numerous warehouse and inventory management apps available that can enhance existing systems or integrate with WMS. This allows warehouse managers to run reports and access key performance indicators (KPIs) on the warehouse floor, enabling them to make informed decisions in real time.
RFID Devices
The use of Radio Frequency Identification (RFID) systems in warehouse management is also on the rise.
While RFID tags are not expected to fully replace barcodes, there are several advantages to using RFID technology. Unlike barcodes, RFID tags do not require a line of sight and can be read and updated. They can also carry more information and enable simultaneous reading of multiple tags, allowing for automatic logging of goods as they enter the warehouse through an RFID portal.
RFID scanners, although specialized devices, are now available as smartphone add-ons, providing a cost-effective solution for businesses looking to leverage RFID technology.
Total Mobile Solutions
While handheld devices alone can significantly boost warehouse performance, further improvements can be achieved by implementing a suite of mobile tools. This includes combining mobile computers and scanners with mobile printers, or pairing a voice solution with a barcode scanner and mobile printer.
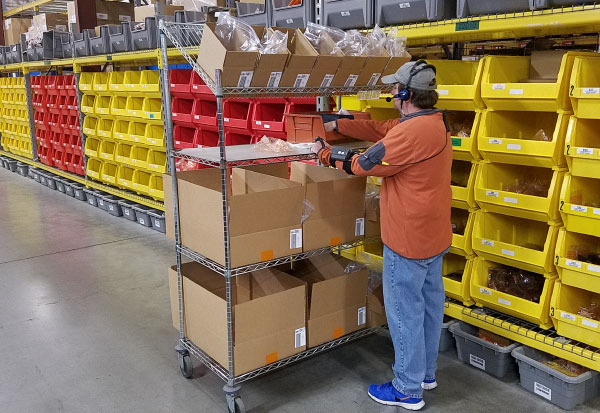
Workers wear lightweight, hands-free devices equipped with microphones and headphones that allow them to communicate directly with the warehouse management system. As orders are received, the system generates voice commands detailing the item location, quantity, and other relevant information.
These commands are transmitted to the worker’s device, and through the use of natural language processing, the worker can verbally confirm their actions or seek clarification.
The device’s speech recognition capabilities ensure accurate interpretation of the worker’s responses, while synthesized speech provides clear instructions, reducing the need for manual reading and minimizing errors.
Choosing the Right Handheld Scanning Device for Your Warehouse
When it comes to selecting the right handheld scanning device for your warehouse, several factors need to be considered. Each warehouse and application will have unique characteristics, but here are some key features and functions to keep in mind:
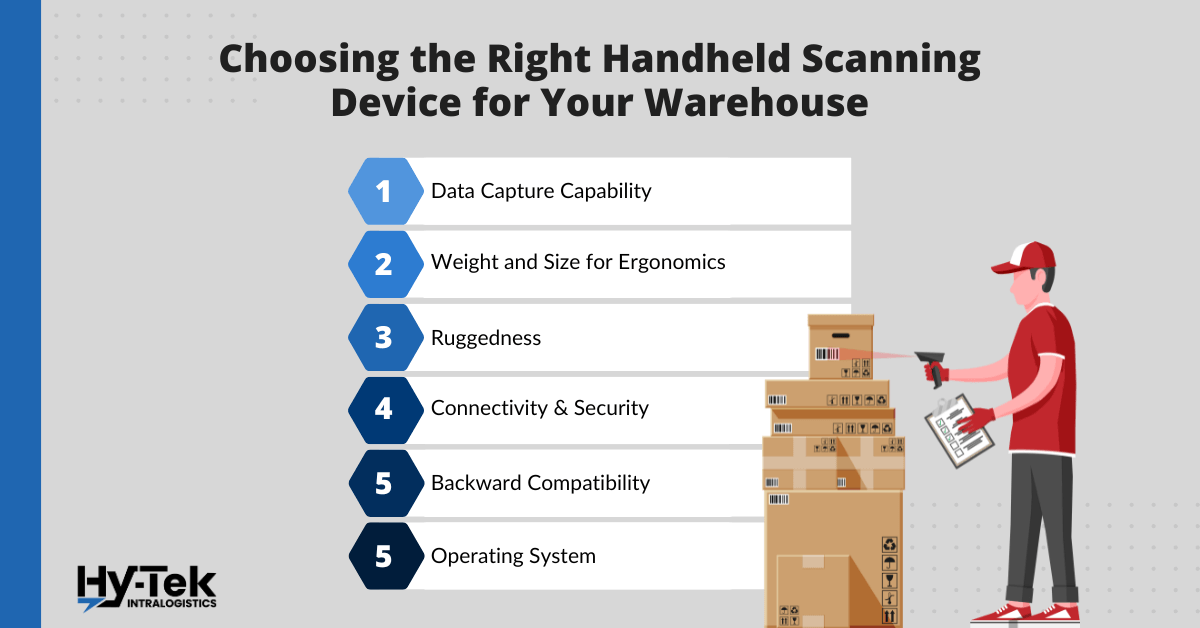
Data Capture
One of the most critical functions of a mobile device in a warehouse environment is barcode scanning. Look for handheld devices that have imager-based barcode scanners capable of scanning both linear and two-dimensional barcodes. These scanners should offer reliable performance at various read ranges, from up close to as far as 70 feet. They should also perform well in high-impact and low-impact scenarios, supporting all the common symbologies in warehouse operations.
Ergonomics
Consider the weight and ergonomics of the handheld device, especially for users who will be carrying it for an entire shift and frequently scanning barcodes. The device should be lightweight and comfortable to hold, without putting strain on the user’s wrist.
For vehicle-mount applications, tablets with separate, long-range barcode scanners may be preferable. Look for devices that offer flexible configurations and the necessary accessories, such as vehicle mounts and holsters, to meet the specific requirements of your use case.
Ruggedness
Warehouses are harsh environments, and handheld devices are prone to drops, moisture exposure, sunlight, and extreme temperatures.
Opt for devices that can withstand drops from up to 5 feet and have an IP rating of IP54 or above, depending on the environment. If your warehouse operates in cold storage conditions, ensure that the device is designed to withstand frost, moisture, and extreme temperatures.
Investing in rugged devices will result in a longer lifespan and lower total cost of ownership compared to consumer-grade devices.
Connectivity
Most warehouses rely on wireless LAN for real-time communication, so it’s essential to choose handheld devices that support the latest Wi-Fi standards and security features such as SOC 2. Additionally, Bluetooth support is necessary for cable-free connectivity to peripherals such as printers. Seamless wireless connectivity ensures fast and easy connection to the back-end network, enhancing productivity and efficiency.
Backward Compatibility
If you already have an existing fleet of handheld devices, consider the backward compatibility of the new devices with your current technology and software. Look for devices that can be easily integrated into your existing infrastructure, potentially using terminal emulation or third-party tools. Ensuring compatibility will help minimize disruptions to your operations and maximize the value of your investment.
Operating Systems
While Windows CE/Windows Mobile was once the go-to choice for warehouse mobile computing, Android has emerged as a viable alternative. Most rugged computer manufacturers now offer Android as an option, thanks to its developer-friendly nature and widespread familiarity among employees. With Microsoft discontinuing support for its old mobile operating systems, a switch to Android may be a cost-effective and future-proof solution for your warehouse.
In conclusion, handheld devices have revolutionized inventory management in warehouses, enabling businesses to improve efficiency, accuracy, and overall productivity. Whether you opt for RF devices, wearables, smartphones, tablets, or RFID systems, choosing the right handheld scanning device for your warehouse requires careful consideration of factors such as data capture capabilities, form factor, ruggedization, connectivity, backward compatibility, and operating system.
By leveraging the power of these devices, you can transform your warehouse operations and unlock new levels of success in inventory management.