A warehouse control system (WCS) is a software application that sends tasks to systems in the warehouse. It tells the systems what task to do to move items and orders from receiving to shipping. A WCS makes sure everything happens in the right order to make the warehouse more efficient.
The WCS sits below the warehouse management system (WMS) and provides real-time execution control of automated equipment such as conveyors, sortation systems, AS/RS cranes, robots, and AGV’s.
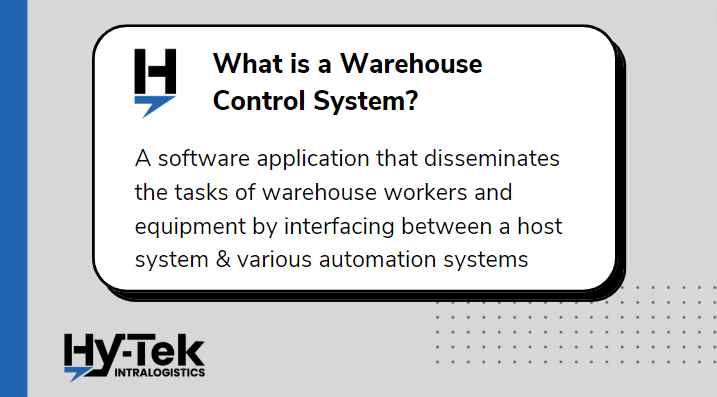
Understanding Warehouse Control Systems (WCS)
Warehouse control systems provide the essential link between WMS software and automated equipment. But what exactly do they do, and how do they work? Let’s take a closer look.
What Does a WCS Do?
A WCS coordinates the movements of materials throughout the warehouse to ensure an efficient and smooth workflow from receiving to shipping while providing real-time directives to operators and equipment controllers for proper product routing and fulfillment.
The WCS is capable of a variety of interface options and can communicate with multiple “Host” Systems. Interface options include FTP, TCP/IP Sockets, ODBC, Shared Table, and Web Service. Custom interfaces are also available.
It accesses data from external sources and then disseminates it to the various floor-level controllers, like a PLC (Programmable Logic Controller), Server, or PC.
The WCS also includes OPC (Open Platform Communication) software that allows it direct communication with Industrial Controllers like a PLC.
This might be necessary for telling the PLC lane assignment for a sorter, pass/fail information for a reject diverter, or any other application that requires WCS-directed routing.
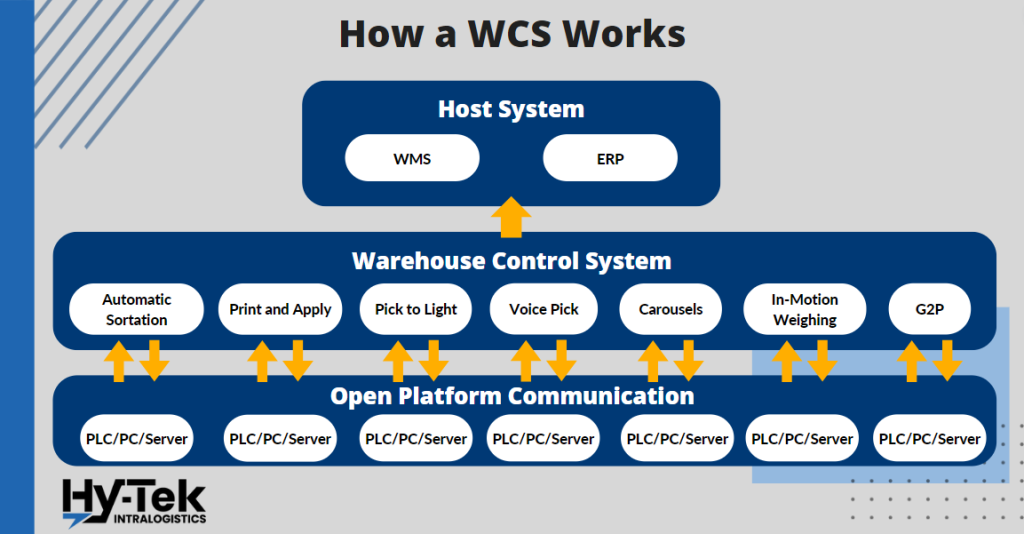
How Does a WCS Work?
Warehouse Control Systems are the middleware that generally sits between the WMS and the floor-level controls for the various “Islands of Automation.” These Islands of Automation include, but are not limited to:
- Automatic Sortation
- In-Motion Print and Apply
- Pick/Put to Light
- Carousels
- In-motion Weighing
- Voice Pick
- Goods-to-person systems
The Host system typically provides the information necessary for the automation to complete its designated functions. This information could include, depending on functionality:
- Order Profile Information
- Exact Lane Assignment
- Labeling Data
- Weight Targets
A WCS not only provides a system to record and store data but also generates reports that fall into three categories: current, history, and maintenance.
Current reports provide statistical performance data such as throughput rates, process totals, errors, and scanner performance rates.
Additional information can be included in the report if it doesn’t affect the functionality of the device but would still offer valuable feedback for the user. Once logged, these reports are moved to History after a predetermined period and archived for future research.
Maintenance reports provide feedback on performance, such as the description of errors, downtime for occurrence, and downtime totals.
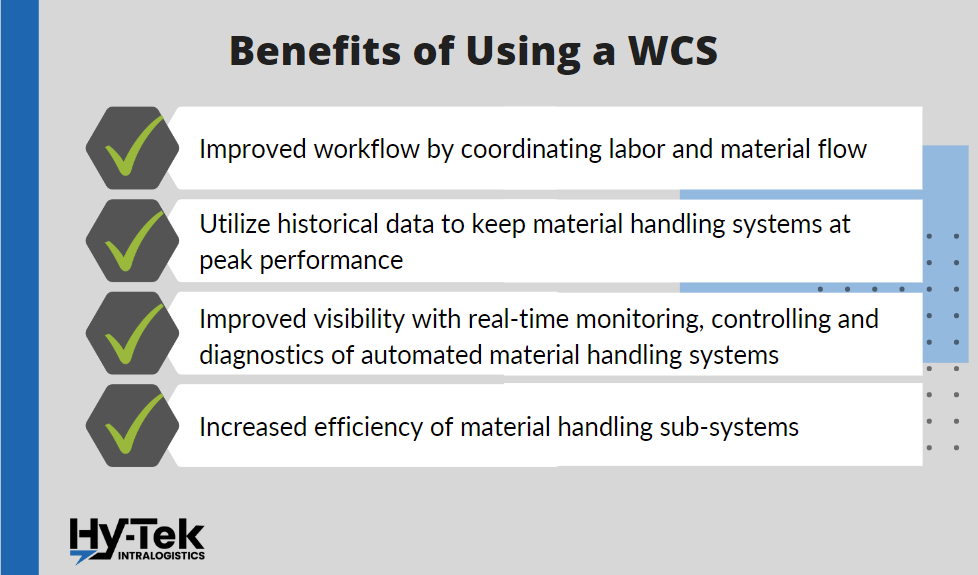
What are the Benefits of Using a WCS?
There are many benefits to using a warehouse control system, including the following:
- Improved Workflow: A warehouse control system can help to improve the overall workflow in the warehouse by coordinating the activities of labor and material flow. This coordination can lead to more efficient use of time and resources, which results in increased productivity.
- Historical Performance Data: It is essential to consistently monitor and assess your warehouse systems’ operational performance to provide your technicians and service staff with clarity into when equipment maintenance is needed. With this data at your fingertips, you can avoid any unexpected downtime or disruptions to your business.
- Improved Visibility: The WCS provides real-time monitoring, controlling, and diagnostics of automated systems based on data collected from system-level controllers and sensors, including real-time views of inventory levels, order status, picking progress, etc. This improved visibility can help to identify problems early on so that corrective action can be taken quickly.
- Increased Efficiency: Increase the efficiency of various material handling sub-systems such as AS/RS and conveyor belts by coordinating material handling systems to determine the most efficient product flow. Additionally, the WCS can be used to optimize storage utilization, leading to decreased operational costs.
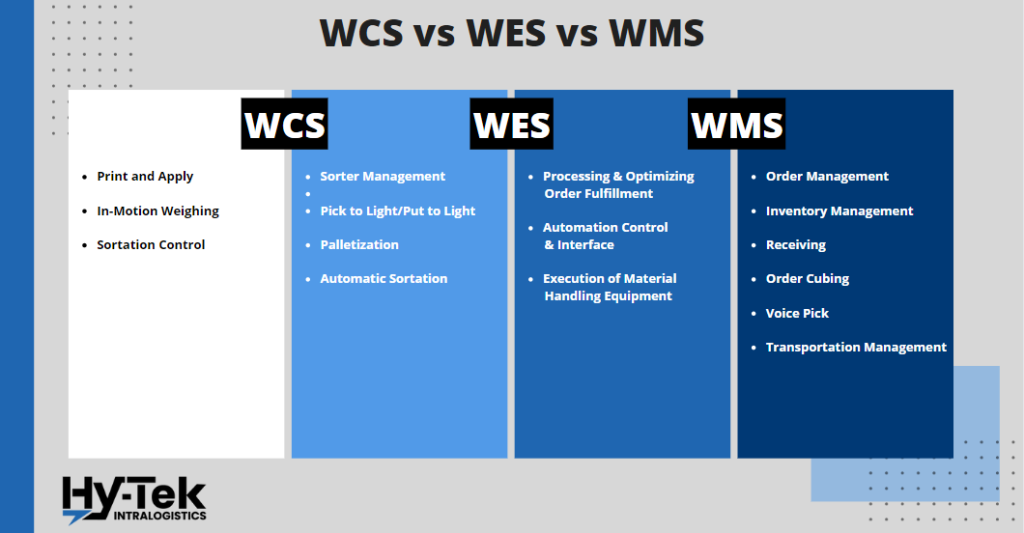
How Does a WCS Differ from a WES and WMS?
It’s important to understand how a warehouse control system differs from a warehouse management system (WMS) or warehouse execution system (WES). We break down the differences between WMS, WCS and WES in greater detail in a separate post, but we’ll cover the basics here.
A WMS oversees the execution of transactions within the four walls of the warehouse, including Receiving, Put-away, Replenishment/Picking, Packing/Shipping, and Inventory Control.
A WCS sits on top of the WMS, providing real-time execution control of automated equipment such as conveyors, sortation systems, AS/RS cranes, robots, and AGVs within the distribution center.
A WES includes planning functionality not found in a WCS that develops an Optimal Execution Plan based on current conditions within the operation, including workforce management, customer orders, inventory levels, transportation plans, etc.
The plan considers real-time constraints such as equipment failures or being understaffed to provide the most efficient path forward.
How to Choose the Right WCS for your Business
When choosing a control system for your business, there are several factors you should consider, including:
- The types of products you store and ship
- The size and layout of your facility
- The number of SKUs you handle
- Your order volume
- Your labor force
- Your budget
You should also consider any future plans you have for expanding your operations. Choosing a WCS that is scalable will ensure that it can grow with your business.
Once you have considered all these factors, you will be in a better position to choose the right WCS for your needs. Doing so could lead to increased efficiency and productivity within your warehouse.
FAQ
What does a warehouse control system do?
A warehouse control system (WCS) sits on top of the warehouse management system (WMS), providing real-time execution control of automated equipment such as conveyors, sortation systems, AS/RS cranes, robots, and AGVs within the distribution center.
What is the difference between WMS and WCS?
A WMS oversees and optimizes broad warehouse processes such as labor management, inventory management, and order fulfillment, while a WCS manages real-time tasks and execution of automated equipment within a warehouse.
What is WCS automation?
A WCS is a software system that integrates with a WMS to provide additional controls and functionality to the warehouse operation. The WCS interacts with and controls the automated equipment within the warehouse, such as: sortation, print and apply, pick to light, carousels, goods to person shuttles and robots arms.