In this digital age, data is the backbone of successful business operations. At the heart of this data-driven approach is the use of Key Performance Indicators (KPIs), which represent critical measurements of business performance.
This is particularly applicable in warehouse management where KPIs for warehouse pickers can mean the difference between efficiency and inefficiency.
Introduction to Key Performance Indicators (KPIs)
Key Performance Indicators (KPIs) are like vital signs for a business, serving as objective metrics to assess its success and effectiveness in achieving its goals.
KPIs are specific, measurable values that act as benchmarks for tracking progress and success in different business areas.
Just as doctors monitor health metrics like heart rate and blood pressure, KPIs help measure and evaluate various aspects of business operations.
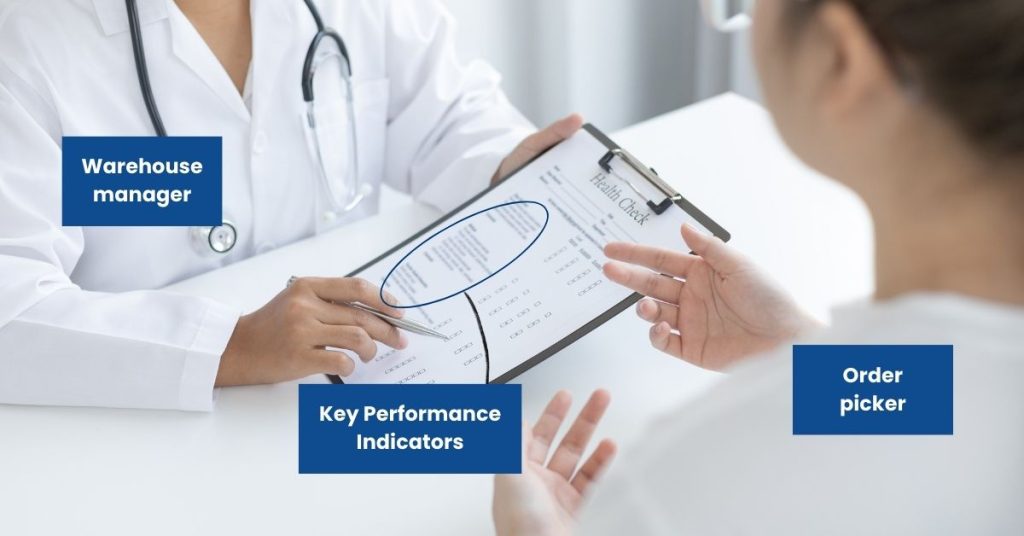
These indicators are tailored to align with the unique objectives and priorities of each company, covering aspects like financial performance, customer satisfaction, employee productivity, and operational efficiency.
Why are KPIs important in a warehouse setting?
KPIs are essential in a warehouse setting because they offer measurable insights into performance, guiding decisions related to inventory management, staff allocation, and equipment investment.
By monitoring and analyzing KPIs, warehouse managers can spot trends and patterns affecting operational efficiency, enabling data-driven adjustments and improvements.
For example, warehouses may track KPIs such as order fulfillment rate, inventory turnover, picking accuracy, and delivery time.
These metrics help identify bottlenecks and areas for enhancement, leading to optimized processes, reduced costs, and improved customer satisfaction.
KPIs also establish a common language and framework for communication and collaboration within the warehouse environment. Clear performance metrics ensure that all stakeholders work together toward common goals, promoting transparency, accountability, and a culture of continuous improvement.
The Role of Warehouse Pickers
Understanding the job of a warehouse picker
Warehouse pickers have a significant role in maintaining the lifeblood of the supply chain.
When it comes to the daily operations of a warehouse, pickers are the backbone of the process. They are the ones who navigate through the aisles, shelves, and racks, carefully selecting the required items for each order. It is a physically demanding job that requires stamina, attention to detail, and excellent organizational skills.
The importance of picking efficiently
Any inefficiency in picking can create a domino effect that disrupts the entire supply chain. It can lead to delays, inaccuracies, frustrated customers, and lost sales.
Hence, a swift and accurate picking process is crucial for overall warehouse productivity.
- Customer Satisfaction: Picking orders efficiently directly impacts the speed of order fulfillment. Customers today expect faster delivery times, and efficient order picking helps meet these expectations. Satisfied customers are more likely to return and become loyal patrons.
- Reduced Lead Times: Efficient picking reduces lead times, which is critical in industries where timely delivery is crucial, such as e-commerce, manufacturing, and retail. Shorter lead times can lead to a competitive advantage.
- Cost Savings: Efficient order picking minimizes labor costs, as less time and effort are required to complete each order. It also reduces the need for overtime or additional staff during peak periods.
- Inventory Accuracy: Accurate picking reduces the likelihood of errors in orders, which can lead to costly returns, replacements, and customer complaints. It helps maintain inventory accuracy, preventing discrepancies between stock levels and what’s recorded in the system.
- Increased Throughput: Efficient picking allows for a higher throughput of orders, which can lead to increased sales and revenue. The warehouse can handle a larger volume of orders without bottlenecks or delays.
- Reduced Stress and Fatigue: Streamlined order-picking processes can reduce stress and physical fatigue among warehouse workers. This can lead to a safer and more pleasant work environment, resulting in lower turnover rates.
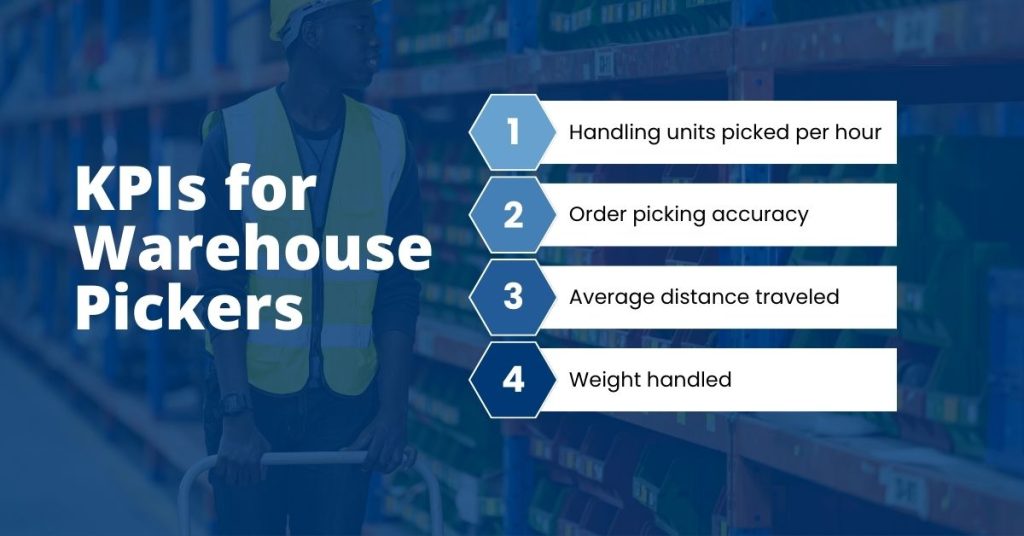
Key Performance Indicators for Warehouse Pickers
Here are some KPIs that are specific to picking operators:
- Handling units picked per hour (i.e. units per hour, cases per hour, pallets per hour)
- Order picking accuracy (error rate)
- Average distance traveled
- Weight handled
How to measure these KPIs
The identification of KPIs is just the first step in evaluating the performance of warehouse pickers. The measurement of these indicators is equally important and can be seen as the critical second step in the process. Various methods can be employed to track and measure these KPIs, depending on the resources and technology available.
A Labor Management System (LMS) is a software solution used in warehouse and distribution center operations to track, manage, and optimize the performance of individual workers or teams. It plays a crucial role in monitoring and improving key performance indicators (KPIs) related to labor efficiency and productivity.
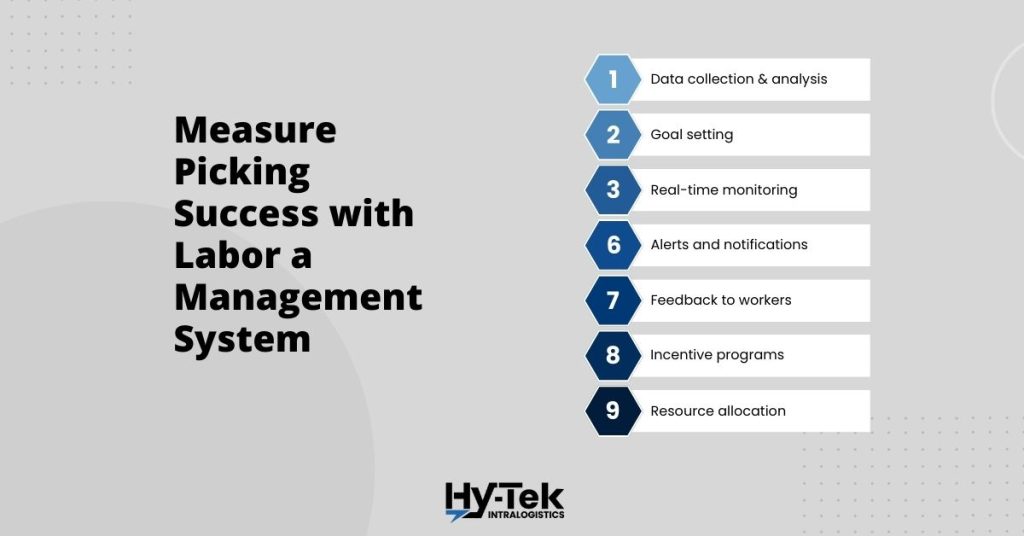
Here’s how an LMS is used to track individual or team KPIs and why you should invest in an LMS:
- Data Collection: The LMS collects data from various sources within the warehouse. This data can include information from barcode scanners, RFID systems, time clocks, and other devices used in the workflow.
- Performance Metrics: The system defines and tracks specific performance metrics or KPIs that are relevant to the warehouse’s goals. These KPIs can vary depending on the nature of the operation but often include metrics like units picked per hour, cases processed per hour, accuracy rates, and time on task.
- Real-Time Monitoring: The LMS provides real-time visibility into individual or team performance. Warehouse managers can access dashboards and reports to see how workers or teams are performing at any given moment. This real-time monitoring allows for immediate action if performance falls below acceptable levels.
- Goal Setting: The system allows managers to set performance goals and benchmarks for individual workers or teams based on historical data and operational needs. These goals are aligned with the warehouse’s broader objectives.
- Alerts and Notifications: If a worker or team falls behind or encounters issues, the LMS can trigger alerts and notifications to warehouse supervisors or managers. This proactive monitoring ensures that problems are addressed promptly.
- Data Analysis: The system analyzes historical data to identify areas of improvement or optimization. It can uncover inefficiencies, bottlenecks, and opportunities for process enhancements.
- Feedback and Coaching: LMS data can be used for performance feedback and coaching. Managers can provide constructive feedback to individual workers or teams based on their KPIs, helping them understand their strengths and areas for improvement.
- Incentive Programs: Many LMS platforms support incentive programs tied to performance. Workers or teams who consistently meet or exceed their KPIs may be rewarded with bonuses, recognition, or other incentives.
- Resource Allocation: The data collected by the LMS can inform resource allocation decisions. If certain teams consistently outperform others, managers may adjust staffing levels or assign tasks accordingly to optimize overall warehouse operations.
- Continuous Improvement: The LMS supports a culture of continuous improvement by providing data-driven insights. Warehouse managers can implement changes and monitor the impact of those changes on KPIs.
There are many labor management systems on the market, and it’s often recommended to have a third-party assess the functionality of any LMS you are considering.
Improving Picker Performance with KPIs
With accurate KPI measurements, you can effectively identify areas of inefficiency, and craft strategies to boost productivity. If picking accuracy is low, you might need to assess picker training procedures or evaluate the clarity of picking instructions.
Strategies for improving picker performance
Improving picker performance involves diverse strategies like:
- Picker training
- System upgrades
- Picking software implementation
- Choosing the right picking method(s) for your business
- Redesigning your warehouse layout for optimal picking paths
Leadership should ensure access to necessary tools and equipment, including basics like gloves and specialized equipment.
Enhancements, such as adding lights to carts or storage racks, improve accuracy and efficiency when using carts. Optimizing productivity involves minimizing unnecessary travel and physical effort while considering ergonomic principles to reduce fatigue.
In terms of technology, warehouses can upgrade from paper-based picking methods to more efficient options like RF scanners or voice picking systems, offering precise guidance and audible instructions.
For even greater productivity gains, advanced technologies like Goods-to-Person (GTP) systems, exemplified by solutions like Exotec, require a higher initial investment but significantly boost pick rates and overall warehouse efficiency.