A warehouse management system (WMS) is a computerized system that helps optimize and automate processes within the warehouse, and according to alliedmarketresearch.com, the WMS market is expected to reach $12.3 Billion in the next 10 years.
There are different tiers of WMS’s that vary in complexity and functionality, however there are some basic functions that any WMS should have.
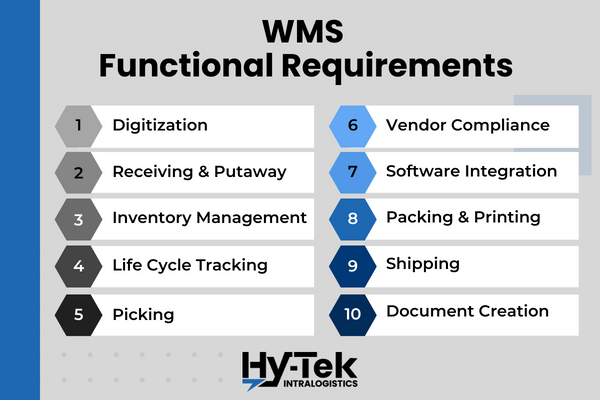
In no particular order, the 10 warehouse management system functional requirements are:
- Digitization
- Receiving & Putaway
- Storage & Inventory Management
- Life Cycle Tracking
- Order Management & Picking
- Vendor Compliance
- Integration with Existing Software
- Packing & Printing
- Shipping
- Document Creation
By choosing the right WMS, you can reduce costs related to manual labor and material handling while also increasing productivity in their supply chain. Moreover, a user-friendly WMS can help improve customer satisfaction by ensuring orders are fulfilled correctly and on time.
1. Digitization
Digitization in warehousing means getting rid of paper and embracing technology like RF scanners to make data entry easier, more accurate and faster. Your WMS should support the digitization effort.
Digitization will also help companies save time and money by having fewer data entry errors, reducing paperwork and automating processes.
Implementing a warehouse management system that promotes digitization is essential for businesses looking to succeed in today’s competitive market.
By utilizing technologies such as RF or Android devices, voice picking, put/pack-to-light, database and ERP connectivity, and automated email notifications, businesses can automate their business processes and eliminate the use of paper Bills of Material (BOM), Bills of Lading (BOL), cut sheets, etc.
2. Receiving & Putaway
A warehouse management system should support receiving functions such as verifying and inspecting incoming shipments, generating item receipts, managing holds, and the following other functions.
Warehouse receiving is more than just ordering inventory and having it sent to your warehouse. A proper process must be followed in order to guarantee that you are getting the correct items and amounts, as well as properly storing them.
- Interface with radio frequency identification (RFID) and devices
- PO / BOL/ Manufacturing receiving and reconciliation
- Manually create a SKU – add a SKU to the database from scanning and advanced shipping notice (ASN)
- Receive ASN
- Manual data entry option
- Directed put away by zone and location
3. Storage & Inventory Management
Warehouse management software systems should provide the necessary tools and features for businesses to have complete control and visibility over their inventory. The system provides inventory visibility by maintaining a real-time, accurate record of the inventory levels in a warehouse. This allows warehouse managers and other staff to see at any given time, how much of each item is in stock, where it is located within the warehouse, and when it is expected to be received or shipped.
- Automated cycle counting – counts should be generated and maintained automatically by the system to enable businesses to manage their warehouse inventory levels accurately and regularly
- Query location inventory – the ability to scan a location and see the items in them, or scan an item and see the location it is supposed to be.
- Inventory tracking – provides real-time data so that items can be located quickly and efficiently within the warehouse
- Directed put away – ensures that products are stored in the optimal location based on factors like size, temperature, whether it’s a fast- or slow- mover, etc.
4. Life Cycle Tracking
Life cycle tracking means tracking the movement of goods from when they are received to when they are shipped out. It is important because it helps ensure that inventory levels remain accurate, and it helps provide better visibility into how inventory is being utilized.
By having accurate records of each product’s journey within the warehouse, businesses can more easily identify problems with shipments and take corrective measures if necessary.
- Lot numbers – should be maintained for each item to enable accurate traceability
- Serial numbers – provides an extra level of detail when tracking a product’s life cycle in the warehouse
- Expiration date tracking – ensures only items that are still within their shelf-life are shipped out
- Manufacturing dates – keep track of stock and ensure that you are not sending out products that have been sitting in storage for too long.
5. Order Management & Picking
It is the responsibility of warehouse managers to ensure that orders are fulfilled correctly and shipped out on time. Picking strategies help to improve order management by optimizing the way goods are chosen from storage spaces and sent to customers.
Warehouse management systems allow businesses to leverage advanced picking strategies that help improve order accuracy and throughput for more efficient operations.
- Batched orders – cart batches, store replenishment vs eCommerce, single and multi-lines, large consignor items
- Wave management – systemically set sizes of waves and auto cutoff
- Labor assignment
- Allocation (pick location)
- Order status
- RF-driven picking – all picking tasks are directed by the RF device
- Optimize pick path – complex pick path that is optimized throughout the distribution center
Featured Resource
[Free Download] WMS Questionnaire
Questions to guide you in your WMS selection process.
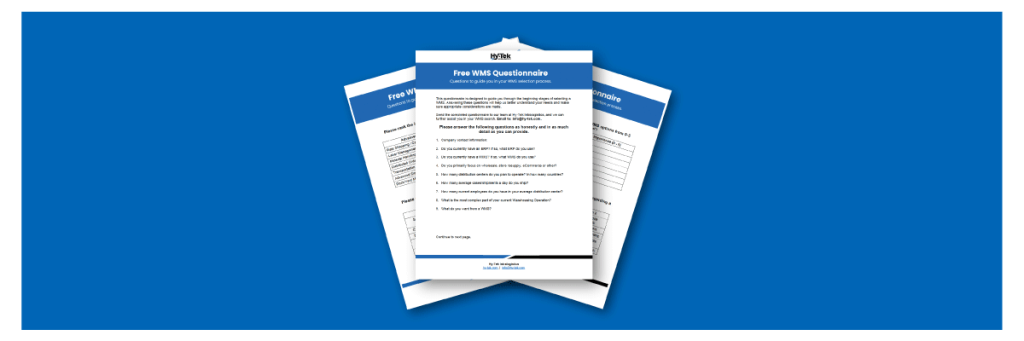
No strings attached. Free download.
6. Vendor Compliance
A WMS can also be integrated with vendor portals that allow for real-time communication and collaboration with suppliers, as well as with EDI (Electronic Data Interchange) systems that enable the exchange of data between the warehouse and vendors in a standardized format – this can help to streamline the order and fulfillment process, and minimize the risk of errors.
- Automated labeling & documentation requirements
7. Integration with Existing Software
A warehouse management system should integrate with other software applications in order to maximize its potential. These applications may include:
- Enterprise resource planning (ERP)
- Customer relationship management (CRM)
- Warehouse execution systems
- Warehouse control systems
- Labor management systems
- Shipping and supply chain solutions
- Accounting software
- Document management systems
- Barcode scanning and tracking software
- Data visualization tools and analytics platforms
Integration of these different types of software allows the warehouse management system to streamline operations by providing real-time visibility into inventory levels and order status. Additionally, it enables businesses to get the most out of their existing resources while reducing costs associated with manual labor.
8. Packing & Printing
Warehouse management software offers a variety of packing and printing capabilities that facilitate a streamlined outbound process.
Many people only pay attention to the ergonomic and storage aspects when designing their packing stations, but to make your packing area even more efficient, you should integrate it with a warehouse management system.
The various packing processes that should be offered by a WMS are:
- Order-based packing
- Pick-to-pack
- Automated packing
- Barcode scanning and labeling
- Palletizing/cartonizing solutions
9. Shipping
A WMS allows for automated order processing and shipping label creation, reducing the need for manual data entry and minimizing errors. Integrating a WMS with shipping sortation technology can increase accuracy and speed of sorting and routing packages for delivery.
A WMS should be able to support the following shipping functions:
- Load consolidation
- Cost tracking
10. Document Creation
A WMS is capable of generating a variety of documents throughout the areas of the warehouse. These documents help keep the warehouse running. Some common documents generated by a WMS include:
- Pick lists – outline the specific items and quantities to be picked for an oder
- Packing slips – a detailed list of the items included in a shipment provided to the recipient
- Bill of Lading (BOL) – A bill of lading (BOL) serves as a contract between the shipper of goods and the carrier transporting them. It lists the details of the shipment, including the type and quantity of goods, the names of the shipper and the recipient, and the shipping details, such as the departure and arrival locations and the expected delivery date.
- Shipping labels – important shipping information such as the recipient’s address and shipping carrier’s barcode
More WMS Considerations
In addition to the warehouse management system functional requirements, there are three features that should be considered when choosing a WMS:
Advanced Warehouse Management System Features
The WMS requirements listed above are the bare minimum requirements, but there are many software solutions that have a higher level of complexity. Some more advanced software features include:
- Cross docking
- Task interleaving
- Returns management
- Parcel shipment management
- Advanced wave management for pick tasking
- Advanced cartonization
- Labor management data capture
Scalability & Flexibility for Future Technology
A scalable and flexible warehouse management system (WMS) is one that is able to grow and change with the needs of a business. It should provide the ability for businesses to easily configure the software in order to accommodate changing requirements, new process flows, or new technologies.
To be future-proof, your WMS should support emerging technologies such as automation, robotics, autonomous robots, voice technology, augmented reality and artificial intelligence.
Additionally, an integrated data platform should allow businesses to capture and analyze relevant data in order to gain insights into customer behavior and market trends. By incorporating these technologies into their WMS solutions, businesses can ensure they stay ahead of the competition and remain agile in an ever-evolving landscape.
User-friendly interface
Having a user-friendly warehouse management system means that the software is intuitive and easy to use. By making sure the system is accessible and easy to learn, businesses can save time and money on training costs while ensuring their employees are able to quickly become productive with the software.
Additionally, having a user-friendly system helps improve job satisfaction among warehouse personnel since they are working with a solution they find both efficient and enjoyable to use.
Finally, user-friendly software also encourages adoption of best practices because it provides an ease of use that makes it easier for employees to do things correctly from the start rather than having to correct mistakes further down the line.
Real-time data
Your warehouse management software should collect real-time warehouse data such as orders, inventory levels, order tracking information, production levels, and personnel performance.
You can then use this data to improve efficiency and accuracy by identifying any bottlenecks or areas for improvement in their process flow.
It can also be used to gain insights into customer behavior and market trends which can lead to better decisions about what promotions or new products to offer.
Finally, this data can also be used to create more accurate forecasts and budgeting in order to prepare for future growth and changes in demand.
Conclusion
It is important to select a solution that meets all of the warehouse management system functional requirements mentioned above. Additionally, the software should be user-friendly and easy to use so that everyone in the warehouse is able to quickly adapt and work with it efficiently. Taking all of these factors into consideration, you can more easily qualify the warehouse management systems that are worth demoing.